Exploring Maintenance Optimization Software Solutions

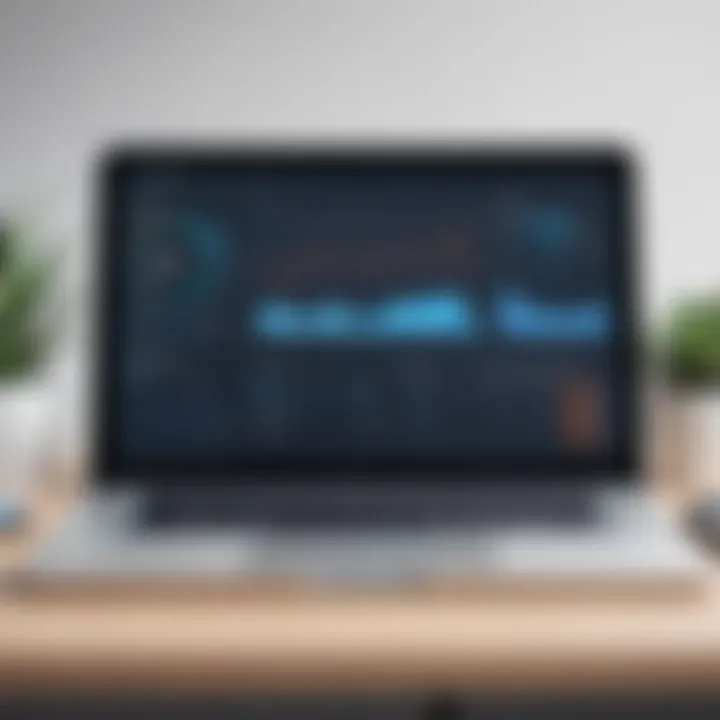
Intro
In recent years, maintenance optimization software has become essential for businesses striving to enhance operational efficiency and cut costs. Various industries rely on these tools to manage their assets effectively, ensuring that equipment and resources function at optimal levels. This software integrates advanced analytics and technology to refine maintenance strategies, making it a pivotal component in today’s competitive landscape.
The continuous evolution in this software category signifies a shift from reactive maintenance to proactive approaches. Companies can analyze data and predict failures before they occur, thereby reducing downtime and increasing productivity. As organizations explore these software solutions, understanding their features and deployment strategies becomes increasingly crucial.
Key Features
Overview of Core Features
Maintenance optimization software typically includes a range of core features designed to improve asset management.
Some notable features include:
- Predictive Maintenance: Utilizing data analytics to forecast equipment failures based on historical performance.
- Inventory Management: Monitoring spare parts and supplies to ensure availability without excessive stock.
- Work Order Management: Streamlining the process of assigning and tracking maintenance tasks.
- Reporting and Analytics: Generating insights on maintenance activities, costs, and equipment performance.
These features contribute to a more proactive maintenance strategy, ultimately leading to improved operational efficiency.
User Interface and Experience
An intuitive user interface is vital for maximizing the effectiveness of maintenance optimization software. The ability to navigate the software smoothly can facilitate user adoption and improve engagement.
Key elements of a user-friendly interface include:
- Dashboard Customization: Allowing users to personalize their view based on preferences and specific needs.
- Mobile Access: Offering mobile applications for technicians and managers to operate on the go.
- Visual Data Representation: Implementing charts and graphs that make interpreting data straightforward.
Maintaining a focus on user experience not only enhances satisfaction but also improves the utilization of available features.
Pricing and Plans
Overview of Pricing Models
Pricing for maintenance optimization software varies significantly. Vendors may offer diverse pricing models, such as:
- Subscription-Based Pricing: Companies pay a regular fee for access to the software, which often includes updates and support.
- One-Time Licensing Fee: A one-time purchase grants perpetual access to the software, with optional maintenance fees for updates.
- Usage-Based Pricing: Costs may fluctuate based on usage metrics, such as the number of users or the volume of data processed.
Comparison of Different Plans
When exploring different plans, businesses should assess the following factors:
- Feature Set: Not all plans may include the same core functionalities.
- Scalability: Ability to expand features or capacity as needs grow.
- Customer Support: Availability of technical assistance and resources.
It's essential to evaluate these parameters carefully to ensure the selected software aligns with organizational goals and operational constraints.
"Understanding the features and pricing models is crucial for decision-makers to make informed choices about maintenance optimization software."
In summary, the exploration of maintenance optimization software offers diverse insights into enhancing operational efficiency and reducing costs. By comprehensively assessing the key features and pricing strategies, businesses can better equip themselves to manage assets effectively. The ongoing advancements in this software domain promise even greater efficiencies and capabilities in the future.
Overview of Maintenance Optimization Software
Maintenance optimization software has emerged as a crucial element in the operational strategy of businesses today. This software focuses on enhancing the efficiency of maintenance practices, leading not only to improved asset management but also to significant cost savings. By centralizing maintenance processes, these systems facilitate better decision-making and streamlined operations.
Defining Maintenance Optimization Software
Maintenance optimization software encompasses various tools and applications designed to help organizations manage their maintenance activities more effectively. These solutions utilize both predictive analytics and data management to optimize the maintenance schedule. The primary goal is to reduce downtime, prolong equipment life, and enhance productivity. Key functionalities include tracking asset performance, scheduling maintenance tasks, and generating reports that inform maintenance strategies.
Importance in Modern Business
The significance of maintenance optimization software in today's business environment cannot be overstated. As organizations increasingly rely on technology, the optimization of maintenance processes becomes vital for sustained operational success.
- It aids in reducing operational costs significantly by minimizing unnecessary maintenance tasks and allocating resources more effectively.
- It enhances productivity by ensuring that equipment is well-maintained and less likely to fail, which supports a seamless operational flow.
- The use of these solutions fosters compliance with industry regulations and safety standards, reducing the risks associated with maintenance errors.
Core Features of Maintenance Optimization Software
Understanding the core features of maintenance optimization software is essential for businesses aiming to enhance their operational efficiency and reduce costs. These software solutions provide centralized tools for managing maintenance processes, enabling organizations to move from reactive to proactive maintenance strategies. Each feature plays a distinct role in solving specific issues encountered in maintenance management.
Predictive Maintenance Capabilities
Predictive maintenance capabilities are one of the most significant aspects of maintenance optimization software. This feature utilizes data analytics and machine learning algorithms to predict when maintenance should be performed. By analyzing historical data, the software identifies patterns that indicate potential failures before they occur. This approach helps in minimizing unexpected downtime and associated costs.
Organizations benefit from predictive maintenance because it allows for better planning of maintenance activities during non-peak times, improving overall resource allocation. Moreover, it extends the lifespan of equipment, as timely interventions prevent major breakdowns. Predictive maintenance is no longer just an advantage; it has become a necessity for organizations looking for a competitive edge.
Asset Management Tools
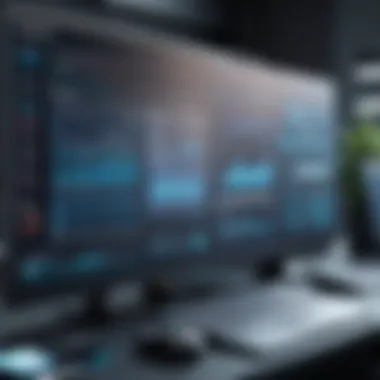
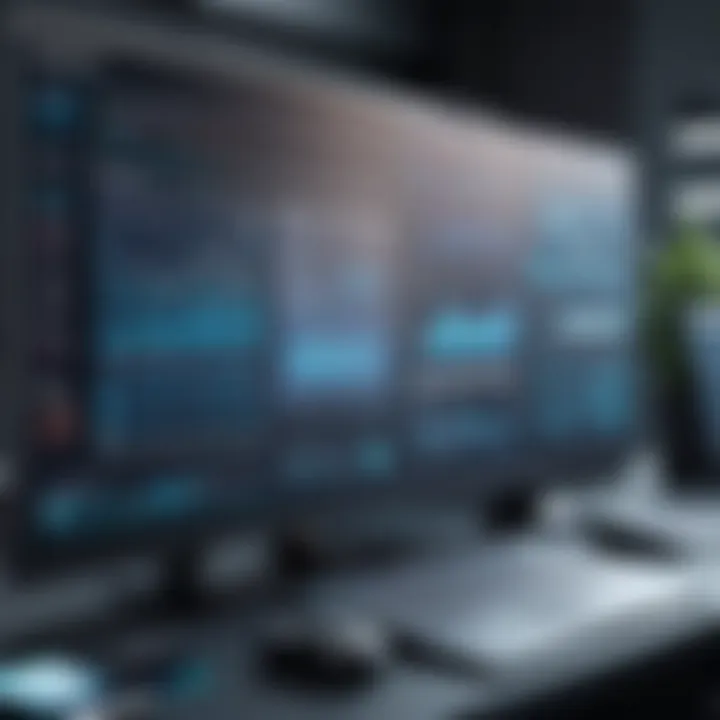
Asset management tools in maintenance optimization software facilitate the tracking and management of an organization’s physical assets throughout their lifecycle. These tools allow for the categorization, tracking, and scheduling of preventive maintenance checks, which enhances accountability and responsibility across the organization.
Using asset management features enables businesses to gain better insights into asset performance and utilization rates. The information gathered helps in financial forecasting and capital expenditure planning. Additionally, it assists in regulatory compliance, ensuring that all assets meet industry standards and regulations. Therefore, effective asset management leads to significant cost savings and an improved return on investment.
Resource Allocation Features
Resource allocation is another crucial feature found in most maintenance optimization software. Effective resource allocation ensures that the right resources are assigned to the right tasks at the right time. This includes labor, materials, and equipment necessary for maintenance tasks.
With advanced scheduling capabilities, the software allows managers to view available resources and plan maintenance activities accordingly. The outcome is a reduction in idle times, which consequently lowers operational costs. By optimizing the use of resources, organizations can improve productivity and ensure that maintenance activities contribute positively to operational goals.
Reporting and Analytics Functions
Reporting and analytics functions are vital components of maintenance optimization software. They allow organizations to generate reports that provide insights into maintenance performance, costs, and other critical metrics. Through intuitive dashboards, users can visualize key performance indicators at a glance.
These functions enable businesses to make data-driven decisions. For instance, by analyzing maintenance history, organizations can identify trends and areas for improvement. This information can help refine strategies and allocate budgets more effectively, ultimately leading to enhanced operational efficiency. In essence, robust reporting tools transform data into actionable insights that drive continuous improvement.
"Maintenance optimization software acts as a fulcrum for operational excellence by streamlining processes, minimizing costs, and extending asset lifecycles."
Benefits of Implementing Maintenance Optimization Software
Implementing maintenance optimization software can substantially transform an organization’s operational framework. This strategic move offers a multitude of benefits that not only enhance productivity but also optimize costs and resources. In a landscape increasingly defined by competition and efficiency, understanding these benefits is crucial for businesses seeking to maintain their edge. The software allows for more informed decision-making practices and provides mechanisms to streamline operations. Here, we discuss several key benefits that arise from successful implementation.
Cost Reduction Strategies
One of the most compelling advantages of adopting maintenance optimization software is the potential for cost reductions. Through predictive analytics and data-driven decision-making, businesses can minimize unexpected failures and reduce downtime. This results in savings on emergency repairs and labor costs. Organizations can effectively monitor their assets, ensuring that maintenance efforts are timely and proportional to need, rather than relying on a reactive approach.
Key strategies include:
- Predictive Maintenance: Using historical data to anticipate failures before they occur, thus preventing costly repairs.
- Resource Allocation: Efficiently distributing resources leads to lower labor costs and minimal waste of materials.
- Inventory Management: Better tracking of spare parts can help avoid excess inventory, thus reducing carrying costs.
By focusing on these strategies, organizations can see a direct correlation between optimized maintenance practices and lower operational costs.
Increased Operational Efficiency
Another significant benefit is the enhancement of operational efficiency. Through the automation of maintenance scheduling and tracking, companies can minimize delays and streamline workflows. This creates a cohesive environment where resources are utilized more productively.
Benefits in this arena include:
- Real-time Monitoring: Allows for immediate adjustment of operations based on current equipment performance.
- Automated Alerts and Notifications: Keeps teams informed and ready to engage in maintenance activities when required.
- Centralized Data Access: Ensures that all relevant stakeholders have instant access to vital information, reducing time lost to searching for data.
The result is an agile organization capable of quickly adapting to changes while ensuring that its assets function at peak capacity.
Enhanced Compliance and Risk Management
Compliance to industry regulations and standards is paramount in many sectors. Maintenance optimization software facilitates adherence to these requirements by providing thorough documentation and tracking capabilities. Organizations can maintain detailed records of maintenance activities, inspections, and compliance audits to demonstrate regulatory compliance.
This enhances risk management in several ways:
- Standardized Processes: Streamlines the inspection routines, reduces errors, and minimizes the risk of non-compliance.
- Documentation: Easier auditing trails are available when records are needed, reducing potential penalties due to lack of compliance.
- Risk Assessment Tools: Identifying and managing risks associated with equipment and operational processes.
With such capabilities, companies are better positioned to manage risks and meet compliance standards effectively.
Improved Equipment Lifespan
The longevity of equipment is directly influenced by how maintenance is conducted. Maintenance optimization software enables a proactive approach that emphasizes regular upkeep and timely interventions. Monitoring the condition and performance of assets extends their life, thereby maximizing the return on investment.
Notable aspects include:
- Condition-Based Maintenance: Adjusting maintenance schedules based on real-time data prolongs equipment life.
- Preventative Measures: Regular servicing identified through data analysis helps in addressing wear and tear effectively.
- Lifecycle Tracking: Understanding the lifecycle allows businesses to time their upgrades more effectively, ensuring that assets are replaced only when necessary.
By leveraging the software's capabilities, organizations can significantly increase the lifespan of their equipment, yielding long-term savings and operational stability.
Types of Maintenance Optimization Software
Understanding the various types of maintenance optimization software is essential for selecting the right tool tailored to specific business needs. Each software category comes with unique features, targeted functionalities, and benefits. They can enhance operational efficiency and foster better asset management practices. Here, the discussion revolves around three primary types: Computerized Maintenance Management Systems, Enterprise Asset Management Solutions, and Predictive Analytics Software.
Each type serves distinct purposes but ultimately contributes to optimizing maintenance processes, decreasing downtime, and ensuring the longevity of assets.
Computerized Maintenance Management Systems (CMMS)
Computerized Maintenance Management Systems, commonly referred to as CMMS, play a crucial role in modern maintenance strategies. CMMS enables organizations to track maintenance activities, manage assets, and streamline workflows.
Key features of CMMS include:
- Work order management: This function allows for the creation, assignment, and tracking of maintenance tasks. Users can prioritize work and ensure that necessary tasks are not overlooked.
- Preventive maintenance scheduling: Rather than leaving maintenance to chance, CMMS enables users to schedule regular maintenance activities based on usage data or time intervals. This reduces emergency repairs significantly.
- Inventory management: Keeping track of spare parts and inventory helps avoid excessive storage costs and ensures that necessary components are readily available when needed.
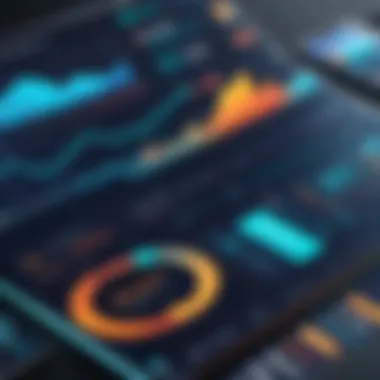
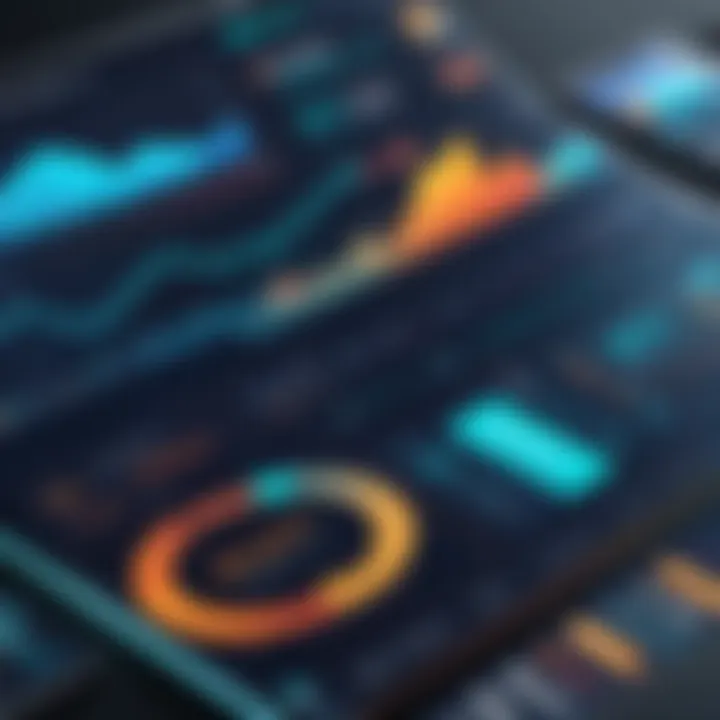
A well-implemented CMMS can result in improved maintenance planning and reduced maintenance costs, making it an indispensable tool for many businesses.
Enterprise Asset Management (EAM) Solutions
Enterprise Asset Management solutions encompass a broader range of functionalities beyond what CMMS offers. EAM solutions integrate various organizational processes, extending their capabilities into financial, operational, and strategic areas.
Benefits of EAM include:
- Holistic asset management: EAM focuses on the entire lifecycle of an asset, from acquisition and operation to disposal. This creates better visibility into asset performance.
- Data-driven decision making: With comprehensive analytics capabilities, EAM facilitates data collection and analysis, improving strategic planning and investment decisions related to assets.
- Compliance and risk management: EAM helps businesses stay compliant with regulations and standards by ensuring maintenance records are well organized and readily available.
By offering these robust functionalities, EAM solutions empower organizations to optimize their asset utilization and enhance overall productivity.
Predictive Analytics Software
Predictive Analytics Software utilizes advanced algorithms and data modeling to forecast equipment failure. This type of software leverages data from various sources, including historical maintenance records and real-time operational data.
Key elements of predictive analytics include:
- Data integration: Predictive software often integrates data from IoT devices, sensors, and other data feeds to identify patterns and trends.
- Failure prediction: It helps predict potential equipment failures, enabling proactive maintenance actions that can prevent unexpected downtimes.
- Continuous improvement: The insights gained from predictive analytics can be used to refine maintenance strategies over time, leading to ongoing improvements in efficiency and reduced costs.
Integration with Existing Systems
Integration with existing systems is a crucial aspect of maintenance optimization software that cannot be overlooked. With businesses relying on various systems, ensuring compatibility is vital for maximizing efficiency and achieving seamless operations. Integration enhances data flow, improves decision-making processes, and supports a more unified approach to maintenance management. Businesses can utilize the insights generated from multiple systems to drive data-driven strategies, leading to better resource allocation and reduced downtime.
ERP System Integration
Integrating maintenance optimization software with Enterprise Resource Planning (ERP) systems is essential for aligning maintenance activities with broader business operations. ERP systems manage crucial business processes, including finance, supply chain, and human resources. When maintenance software integrates seamlessly with ERP, it allows for:
- Improved visibility across departments,
- Streamlined communication, and
- Harmonized budgeting and resource planning.
This integration not only enables the sharing of real-time data but also ensures that maintenance workflows are aligned with financial and operational priorities. Businesses can analyze the financial impact of maintenance decisions and derive insights that promote cost-effectiveness.
IoT Compatibility
The Internet of Things (IoT) is reshaping how industries approach maintenance management. Maintenance optimization software that is compatible with IoT devices can provide a tremendous advantage. Devices equipped with sensors can monitor equipment in real-time, collecting data on performance and anomalies. This integration enables:
- Real-time monitoring of asset conditions,
- Timely alerts for preventive measures, and
- Enhanced predictive maintenance analytics.
By leveraging IoT data, organizations can transition from traditional maintenance approaches to more proactive strategies. This capability not only minimizes unplanned downtime but also extends the lifespan of assets.
Data Migration Challenges
One cannot ignore the challenges associated with data migration when implementing maintenance optimization software. Smooth migration is critical to maintaining data integrity and ensuring continuity in operations. Common hurdles include:
- Data quality issues: Ensuring that data is accurate and complete before migration.
- Compatibility problems: Identifying potential discrepancies between old and new systems.
- Resource allocation: Dedication of time and personnel to oversee the migration process.
Planning for these challenges involves conducting thorough assessments of existing data. By understanding the quality and structure of current data, organizations can establish a viable migration strategy. Training teams to handle migration effectively will also foster a smoother transition, ultimately driving successful integration of maintenance optimization software.
Best Practices for Implementing Maintenance Optimization Software
Implementing maintenance optimization software successfully requires careful planning and execution. This section focuses on effective strategies that can transform how businesses utilize such systems. By understanding the best practices, organizations can maximize the potential of these tools, driving better asset management and paving the way for enhanced operational efficiency.
Assessment of Business Needs
The first step in implementing maintenance optimization software is to conduct a thorough assessment of your business needs. This involves examining current maintenance practices, identifying inefficiencies, and understanding the specific goals you aim to achieve with the software.
A clear understanding of your requirements helps in selecting the right software that aligns with organizational objectives. For instance, if an organization experiences frequent equipment breakdowns, focusing on predictive maintenance features will be crucial. Additionally, stakeholders must consider factors such as:
- Budget constraints: Identify how much can be allocated for software, training, and ongoing support.
- Scale of operations: Understand whether the software will be used across multiple sites or just one.
- Integration requirements: Assess how the new software will work with existing systems, like ERP solutions.
This assessment ensures that the selected software not only meets immediate needs but also positions the organization for long-term success.
User Training and Support
Once the software is chosen, investing in user training cannot be overlooked. This step is significant in guaranteeing that personnel can effectively use the software’s features. Without adequate training, even the most advanced software can fall short of expectations.
Consider implementing the following strategies:
- Hands-on training sessions: Organize workshops where users can interact with the software under expert guidance.
- User manuals and documentation: Provide detailed written materials for reference, ensuring users have a resource when questions arise.
- Ongoing support: Establish a clear communication channel for addressing user queries post-implementation.
A well-supported training program fosters a culture of competence and confidence among users, making it easier for them to adapt to the new system.
Continuous Improvement and Feedback Loops
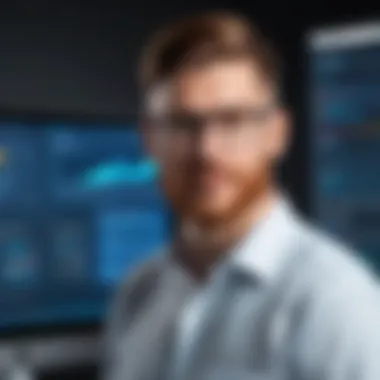
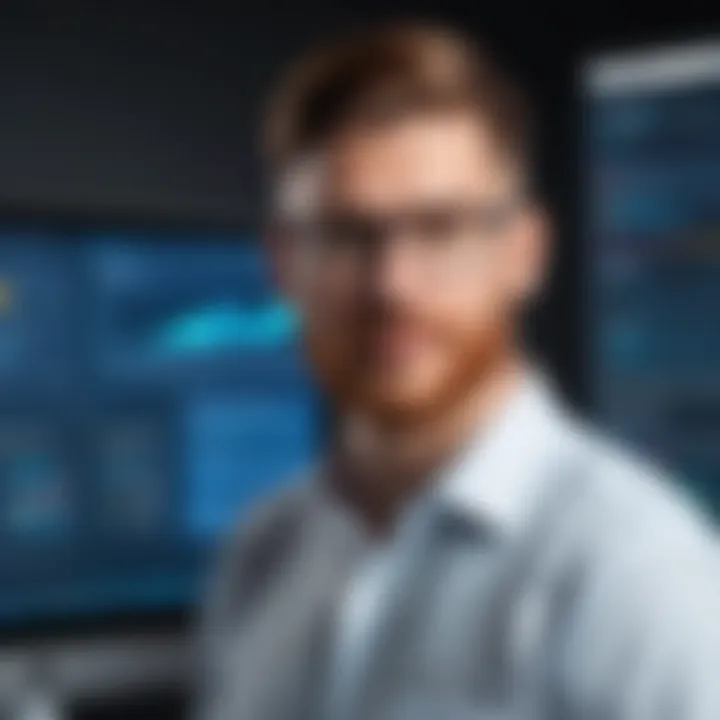
The implementation of maintenance optimization software should not be seen as a one-time process. Instead, it should involve continuous improvement and refinement based on user feedback and evolving business needs. Establishing feedback loops enables organizations to capture insights directly from users.
Engaging employees who interact with the software daily can provide valuable information on:
- Usability issues: Identifying challenges that might not have been apparent during training.
- Performance metrics: Understanding how the software impacts maintenance efficiency and asset management.
- Feature requests: Gathering suggestions for additional functionalities that could enhance the user experience.
Adopting a mindset of ongoing improvement encourages adaptability and ensures that the software evolves alongside the business, thus maximizing its effectiveness.
"Successful implementation of maintenance optimization software requires clear strategies and active engagement from all stakeholders involved."
By adopting these best practices during implementation, organizations lay a solid foundation for leveraging maintenance optimization software effectively. Ultimately, this leads to improved decision-making, operational efficiency, and cost savings.
Challenges in Using Maintenance Optimization Software
The implementation of maintenance optimization software can bring significant advantages to businesses, however, it does not come without challenges. Understanding these challenges is crucial for organizations aiming to fully harness the benefits of these systems. In this section, we discuss three primary challenges: change management issues, cost considerations, and technology adaptation barriers.
Change Management Issues
Change management is a vital aspect that organizations must address when introducing maintenance optimization software. Employees often resist new technologies due to fear of the unknown or a belief that their skills may become obsolete. This can lead to decreased morale, which negatively impacts the project. To combat this, businesses should focus on effective communication, outlining the benefits of the new system clearly. Involving employees in the selection and implementation process can foster a sense of ownership and mitigate resistance. Moreover, developing a solid change management strategy that includes training programs can ease transitions.
Cost Considerations
Cost is a critical factor for many businesses looking to adopt maintenance optimization software. Initial investments often include software purchase, licensing fees, and potentially hiring additional consultants for implementation. Ongoing costs such as subscription fees and maintenance can add up, impacting budgets. Therefore, it’s essential for organizations to conduct thorough financial analyses to assess return on investment. Beyond just monetary expenses, organizations should consider the opportunity costs lost during the implementation phase. Engaging in pilot programs can help to demonstrate potential savings and operational efficiencies before committing to a full-scale rollout.
Technology Adaptation Barriers
Technology adaptation barriers can significantly stall the success of maintenance optimization software. These barriers may arise from issues such as outdated infrastructure, lack of compatibility with existing systems, or skill gaps within the workforce. Businesses often face circumstances where legacy systems are deeply integrated into day-to-day operations, making it difficult to adopt new solutions. To overcome these barriers, organizations must assess their current IT landscape and ensure the new software can integrate seamlessly. Investing in training and upskilling employees can also enhance adaptability, paving the way for more successful implementation. By addressing these issues proactively, organizations can enhance their operational efficiency.
"Understanding and addressing the challenges of maintenance optimization software implementation can minimize risk and maximize benefits."
Ultimately, acknowledging these challenges during the planning process can help companies refine their approach. By doing so, they can better prepare for potential pitfalls and ensure a smoother transition. Identifying these obstacles beforehand also provides opportunities to develop targeted strategies to mitigate risks, thus improving the overall chances of successful software integration.
Case Studies: Successful Implementation
The realm of maintenance optimization software is replete with instances where effective implementation has led to transformative results. Understanding these case studies provides critical insight into the application of such solutions across different industries. Each example showcases specific elements and benefits, emphasizing real-world applications that drive the discussion forward. By analyzing successful implementations, businesses can glean best practices, potential pitfalls to avoid, and strategies for maximizing effectiveness.
Manufacturing Sector Examples
In the manufacturing sector, companies face a myriad of challenges, including equipment downtime, maintenance costs, and resource management. Case studies from this area illustrate how maintenance optimization software can significantly streamline operations. For example, a large automotive manufacturer integrated a Computerized Maintenance Management System (CMMS) that facilitated predictive maintenance.
This system allowed for the collection of data from various machines, predicting potential failures before they occurred. As a result, the manufacturer reported a 30% decrease in unplanned downtime, directly boosting production efficiency. Additionally, the implementation of resource allocation features helped optimize staff schedules, resulting in better labor management and reduced overtime costs.
Some key points to note from this case study include:
- Data-Driven Decisions: Using real-time data led to informed maintenance schedules.
- Cost Efficiency: Reduced downtime significantly impacted the bottom line positively.
- Scalable Solutions: Adapting the software as the company's needs evolved proved essential.
Facilities Management Use Cases
Facilities management presents unique challenges, particularly in managing various assets across large properties. A notable case can be seen in the use of maintenance optimization software by a large hotel chain. The implementation of Enterprise Asset Management (EAM) software streamlined their maintenance processes by improving visibility across their assets.
With this software, the hotel chain was able to track maintenance history and schedule preventive maintenance, which resulted in an impressive 25% reduction in emergency repairs. This proactive approach preserved the quality of facilities and elevated customer satisfaction. The ability to manage preventive measures reduced overall maintenance costs and minimized disruptions for guests.
Highlights from this case study include:
- Long-term Planning: Anticipating repairs led to more successful budget management.
- Resource Management: Efficiently allocating staff for maintenance tasks improved operational workflow.
- Customer Impact: Enhanced facilities encouraged repeat business and positive reviews.
These case studies underscore the tangible benefits of maintenance optimization software. They highlight not only efficiencies and cost savings but also the broader impact on customer satisfaction and business sustainability. Each example serves as a roadmap for companies looking to enhance their maintenance strategies effectively.
Future Trends in Maintenance Optimization Software
Understanding the future trends in maintenance optimization software is crucial for businesses aiming to stay competitive. As technology evolves, organizations must adapt to these changes. Embracing future advancements enables improved efficiency and better resource management. The software plays a vital role in how businesses approach maintenance tasks, and following new trends ensures they are equipped to mitigate potential risks.
The Role of Artificial Intelligence
Artificial Intelligence (AI) is becoming increasingly significant in maintenance optimization software. AI algorithms analyze vast amounts of data, providing insights that help predict equipment failures and maintenance needs. This predictive capability not only reduces downtime but also minimizes maintenance costs, which is a primary concern for businesses today.
- Enhanced Decision-Making: Using AI enables more informed decisions based on data-driven insights.
- Automation of Routine Tasks: AI automates many routine maintenance tasks, freeing human resources for more complex issues.
- Resource Optimization: Effective deployment of resources helps in maintaining equipment longevity and operational efficiency.
Incorporating AI into maintenance processes can lead to smarter operational frameworks, allowing businesses to optimize performance systematically. Companies that adapt to these innovations position themselves for future success.
Advancements in Predictive Maintenance Technologies
Predictive maintenance technologies have seen notable advancements in recent years. These developments offer new ways to enhance the accuracy and effectiveness of maintenance initiatives. Traditional methods often relied on scheduled maintenance, which may not have always been necessary. In contrast, predictive maintenance uses real-time data to forecast when equipment might fail. This can lead to:
- Significantly Reduced Downtime: Scheduled interventions are replaced by need-based actions.
- Cost Savings: Fewer unnecessary repairs or replacements reduce overall operational costs.
- Increased Asset Lifespan: Addressing issues before they escalate ensures equipment operates longer and more efficiently.
Engaging with modern predictive maintenance technologies allows businesses to derive substantial value from their assets. By focusing on data analytics, organizations can determine optimal maintenance intervals and reduce reactive maintenance actions, thus enhancing operational efficiency.
"Incorporating AI and advancements in predictive technologies provides businesses with more control and insight over their maintenance strategies."
Businesses that invest in these technologies will find themselves at the forefront of their industries. The trends in maintenance optimization software indicate a paradigm shift, emphasizing proactive approaches and data intelligence. Adapting to these changes can greatly enhance an organization's performance and resilience.