Understanding Fabrication Shop Software for Efficiency
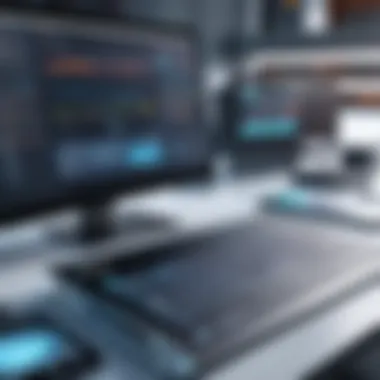
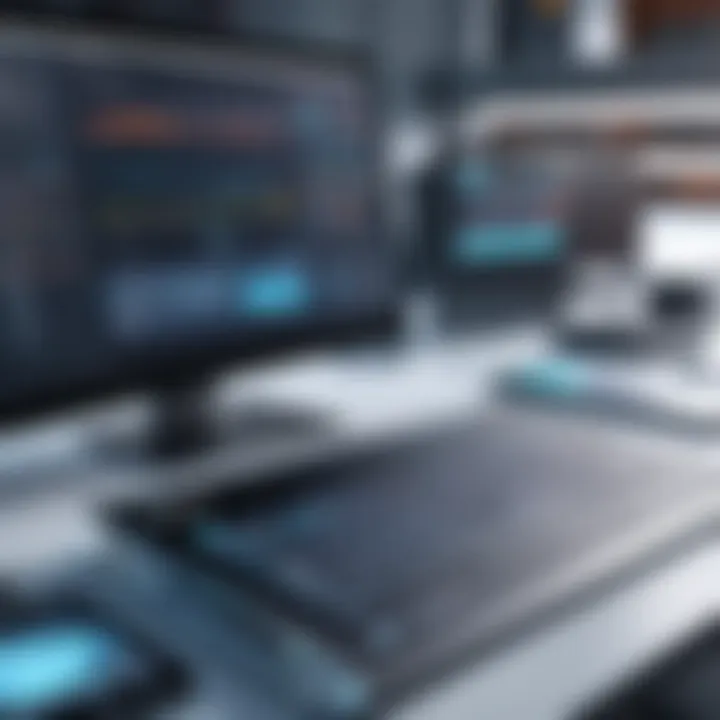
Intro
Fabrication shop software plays a crucial role in modern manufacturing environments. As businesses strive to improve operational efficiency, this software emerges as a vital tool. Whether it's about managing resources, optimizing workflows, or enhancing productivity, understanding the intricacies of fabrication shop software is essential for decision-makers. In this article, we will explore its core features, benefits, pricing, and how it can be tailored to specific industries.
Key Features
Overview of Core Features
Fabrication shop software encompasses a variety of functionalities designed to streamline processes. Some of the core components often include:
- Job Management: Allows businesses to track orders, deadlines, and resources, ensuring smooth project flow.
- Inventory Management: Helps monitor stock levels, manage supplies, and prevent shortages.
- Quoting and Estimation Tools: Facilitates accurate price quotations based on materials and labor, improving financial planning.
- Reporting and Analytics: Provides insights into operational performance, identifying areas for improvement.
- Integration Capabilities: Supports connection with other software systems, enhancing data flow and coordination.
Each of these features contributes to a more organized and efficient work environment. They reduce manual errors and provide better visibility into operations.
User Interface and Experience
The usability of fabrication shop software is pivotal. A user-friendly interface can significantly reduce training time and increase team adoption. Most software options prioritize intuitive design, ensuring that users can navigate easily. Key elements to consider include:
- Dashboards: Visual representations of key metrics.
- Customization Options: Ability to tailor the interface based on individual user requirements.
- Mobile Compatibility: Some platforms offer apps to manage operations on-the-go, crucial for fast-paced environments.
A well-designed user experience directly correlates with productivity. When teams can access information quickly and efficiently, the entire shop benefits.
Pricing and Plans
Overview of Pricing Models
The pricing for fabrication shop software varies widely based on features and capabilities. Common models include:
- Subscription-Based: Monthly or annual fees provide access to software, often including updates and support.
- One-Time Purchase: A lump sum payment for perpetual licenses, though this may incur additional costs for updates.
The decision on which model to choose often depends on budget flexibility and long-term operational needs.
Comparison of Different Plans
Evaluation of various software plans is essential. When comparing options, businesses should consider:
- Feature Set: Does the plan include all necessary features for your specific context?
- Scalability: Will the software grow with your business?
- Support Services: Are technical support and training included in the price?
Making an informed decision requires weighing these criteria against organizational needs.
"Investing in the right fabrication shop software can significantly enhance productivity and reduce overhead costs."
Overall, operating within the fabrication industry demands efficient tools, and software solutions fulfill this requirement effectively. By leveraging features, pricing models, and user experience, businesses can make informed choices that lead to increased productivity.
Prologue to Fabrication Shop Software
In today's competitive manufacturing landscape, businesses must leverage every advantage available to them. Fabrication shop software plays a vital role in improving operational effectiveness. This software is designed to streamline processes, helping shops manage various aspects such as job tracking, inventory control, and quoting.
This section provides an overview of what fabrication shop software is and its significance in a fabrication environment. Understanding this software is crucial for decision-makers and IT professionals who are investing in technology aimed at enhancing efficiency and reducing costly errors.
Definition of Fabrication Shop Software
Fabrication shop software refers to computer programs tailored to meet the specific needs of manufacturing and fabrication facilities. These programs typically include modules for job management, inventory oversight, and scheduling, among other functions. By automating various tasks, this software aims to facilitate smoother operations and reduce the time spent on manual processes.
Fabrication shop software can genuinely transform how a shop operates. It integrates disparate processes into a single, cohesive platform, thus enabling better communication and collaboration among teams.
Importance of Software in Fabrication Shops
The role of software in fabrication shops cannot be overstated. First, the software enhances efficiency by automating time-consuming tasks. For example, tracking jobs manually can introduce errors and inefficiencies. With the right software, shops can maintain up-to-date records, improving accuracy and accountability.
Second, the software aids in better decision-making. Reporting and analytics features allow business owners to analyze performance metrics, understand labor costs, and optimize inventory management. Armed with this information, decision-makers can identify areas for improvement and take actionable steps.
"Investing in effective shop management software is crucial for sustained growth and success in the fabrication industry."
Finally, the integration capabilities of fabrication shop software are paramount. Whether it’s ERP, accounting, or CRM systems, ensuring compatibility can drive productivity and lead to better operational practices. As shops evolve, the capacity for software to adapt to new challenges and innovations is essential for maintaining a competitive edge.
Core Features of Fabrication Shop Software
The core features of fabrication shop software are critical in enhancing the operation and overall management of the fabrication process. By leveraging these functionalities, businesses can streamline several aspects of their operations. Each feature contributes uniquely to improving efficiency, accuracy, and productivity, which are vital in a competitive market. Understanding these features enables shop owners to select software that best meets their specific needs and the dynamic environment of a fabrication shop.
Job Management and Tracking
Job management and tracking is an essential feature in fabrication shop software. This function allows businesses to monitor all projects throughout their life cycles. With job tracking, managers can easily see the status of ongoing work, assign tasks to employees, and ensure that deadlines are met. An effective job management module simplifies workflow by providing real-time updates on job progress.
Moreover, the integration of tracking tools enables shops to identify bottlenecks and inefficiencies in their processes. By analyzing job data, companies can make informed decisions aimed at improving overall performance.
Inventory Management
Inventory management is another vital element of fabrication shop software. Efficient inventory tracking ensures that raw materials are available when needed without overstocking. Software can monitor the levels of materials in real time, alerting users when it is time to reorder supplies. This not only reduces waste but also lowers carrying costs associated with excess inventory.
An added benefit is the ability to manage suppliers and track variability in material costs. Equipped with accurate data, fabrication shops can make better purchasing decisions and negotiate better terms, ultimately leading to significant cost savings.
Quoting and Estimating Tools
Quoting and estimating tools are essential for accurate pricing in fabrication projects. This feature enables businesses to generate quotes quickly based on precise calculations derived from existing data. Utilizing templates tailored to specific project types enhances efficiency and reduces human error.
With robust quoting mechanisms, teams can factor in materials, labor, and overhead costs to produce comprehensive estimates. This functionality not only fosters transparency in pricing but also reinforces trust with clients. Accurate estimates can facilitate quicker approval cycles and enhance customer satisfaction.
Scheduling and Resource Allocation
One of the most significant challenges in a fabrication shop is effective scheduling. The scheduling and resource allocation feature optimizes workflow by ensuring that the right resources are available at the right time. This can include equipment, personnel, and materials, all of which need to align perfectly to achieve production goals.
By utilizing advanced scheduling tools embedded in the software, shops can visualize workloads and priorities. Functionality like calendar integration and automatic reminders ensures all stakeholders are aware of task deadlines and responsibilities, thereby minimizing downtime and enhancing productivity.
Reporting and Analytics
The reporting and analytics feature is invaluable for performance evaluation. This function allows businesses to generate detailed reports about various aspects of their operations. It provides insights into productivity metrics, project costs, and profitability.
Analytics tools help management identify trends and areas for improvement. By reviewing historical data, shops can predict future demands and allocate resources accordingly. In this manner, reporting not only serves as a retrospective analysis but also as a guide for strategic planning and decision-making.
"Fabrication shop software equipped with robust core features transforms operational processes, resulting in measurable gains in efficiency and profitability."
These core features of fabrication shop software serve as the backbone of an effective operational strategy. They are designed to elevate the capabilities of fabrication shops, making them more competitive and robust in the face of industry challenges.
Benefits of Utilizing Fabrication Shop Software
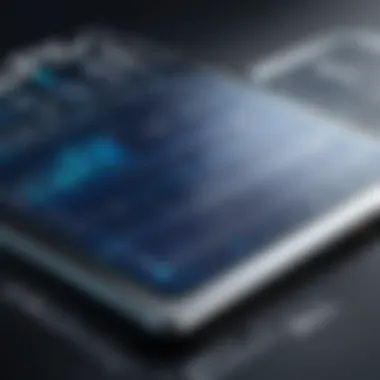
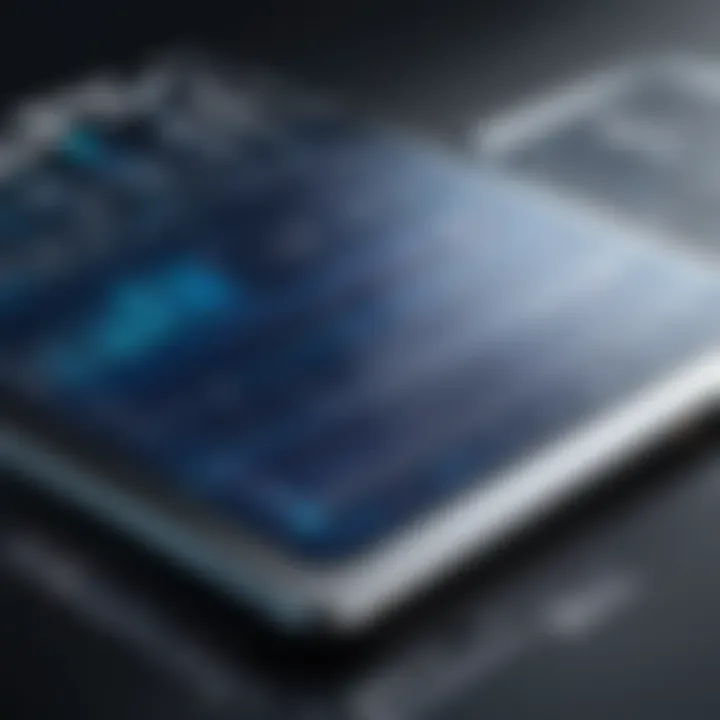
The utilization of fabrication shop software provides numerous advantages that can significantly impact productivity and cost-efficiency. In modern manufacturing environments, businesses seek ways to streamline operations and enhance their competitive edge. Here, we explore essential benefits that fabrication shop software delivers, elucidating its importance in today’s context.
Enhanced Operational Efficiency
Operational efficiency is critical in any manufacturing setting. Fabrication shop software enhances this aspect by automating repetitive tasks that would otherwise consume valuable time and resources. For instance, through job management modules, managers can assign and track tasks seamlessly. This leads to reducing delays and improving load balancing across various teams.
Furthermore, real-time monitoring features allow managers to address issues as they arise, minimizing downtime. By implementing software that integrates all processes, from quoting to production, companies can optimize workflows, making them significantly more effective.
Improved Accuracy in Estimates
Accurate estimates are vital for maintaining competitiveness and customer satisfaction in fabrication shops. Fabrication shop software includes quoting and estimating tools that ensure precision through standardized templates and automated calculations. This reduces human error, which is common in manual processes.
Using historical data and project specifics, the software can generate reliable estimates for time and materials needed. Such accuracy can enhance customer trust and satisfaction, ultimately leading to higher contract acceptance rates.
Streamlined Workflow Processes
Streamlined workflows are fundamental for maximizing output in fabrication environments. Fabrication shop software consolidates communication and data flow, facilitating a smoother transition between different stages of production. Instead of teams working in silos, everyone is connected through centralized data access.
For example, the software can notify team members of changes in deadlines or requirements instantly, ensuring that all employees are aligned with the project's objectives. This integration minimizes confusion and redundant efforts, resulting in a cohesive operation that can rapidly adapt to changes.
Increased Profit Margins
Lastly, the financial benefits of adopting fabrication shop software are compelling. By increasing efficiency and accuracy, businesses can reduce overhead costs associated with waste, rework, and delays. The time saved in managing jobs and estimating costs translates directly into savings and ultimately leads to increased profit margins.
Moreover, enhanced data analytics and reporting facilitate better decision-making regarding pricing strategies and operational improvements. Through careful analysis of costs versus profits, business owners can fine-tune their approach to maximize revenue across various projects.
"Investing in fabrication shop software is not merely about cost; it’s about creating a roadmap for sustainable growth and efficiency."
Implementing fabrication shop software is not just a trend; it is a strategic move that can yield tangible benefits. As the industry evolves, businesses that leverage software solutions will likely outperform those that do not.
Types of Fabrication Shop Software
The landscape of fabrication shop software is diverse, comprising various solutions tailored to meet different operational needs. Understanding the types of these software solutions is crucial for business owners and decision-makers aiming to optimize their processes. Each type offers unique advantages, which can significantly affect the overall efficiency and productivity of fabrication shops.
Standalone Software Solutions
Standalone software solutions are self-contained applications designed to perform specific tasks without relying on other systems. These programs can effectively manage particular segments of a business, such as job tracking or inventory control.
Benefits of standalone solutions include:
- Cost-Effectiveness: Typically, these solutions require lower upfront investments compared to larger integrated systems.
- Simplicity: They often feature user-friendly interfaces that allow employees to learn and adapt quicker.
- Focus on Specific Functions: Businesses can choose software that specializes in their most pressing needs, such as scheduling or quoting.
However, one challenge can be the lack of communication between different standalone applications. This limitation can lead to inefficiencies when data needs to be transferred between systems.
Integrated Software Systems
In contrast, integrated software systems combine various functionalities into one cohesive platform. These applications synchronize job management, inventory control, and reporting into a unified system. An integrated approach provides a more holistic view of operations, enabling better decision-making.
Key advantages of integrated systems include:
- Seamless Data Flow: Information shared across the platform reduces errors associated with data entry and enhances real-time decision making.
- Comprehensive Reporting: Factoring in various metrics can lead to more informed strategies, promoting operational efficiency.
- Reduced Complexity: One system means fewer training sessions, as employees need to familiarize themselves with only one application.
Despite these advantages, integrated systems can be pricier and may require more time in terms of setup and training.
Cloud-Based Versus On-Premise Software
When selecting fabrication shop software, businesses often face a choice between cloud-based or on-premise solutions.
Cloud-Based Software involves hosting applications on external servers, allowing access from any internet-enabled device. This option offers flexibility, automatic updates, and minimal initial investment.
Benefits include:
- Accessibility: Employees can work remotely, providing agility in managing operations.
- Scalability: Companies can easily upgrade or downgrade their services based on current needs.
- Cost-Efficiency: Typically, these solutions operate on a subscription model, reducing the financial burden of large one-time payments.
On-Premise Software, on the other hand, is installed locally on a company’s servers. While this option grants complete control over data security and often offers customizable features, it comes with significant responsibilities.
Potential drawbacks are:
- Higher Initial Costs: Businesses must invest in hardware and software purchases upfront.
- Maintenance Responsibility: Companies need to manage updates and security, potentially stretching internal IT resources.
- Limited Accessibility: Employees may be restricted to office settings unless arrangements are made for remote access.
In summary, the choice between cloud-based and on-premise software largely depends on a business’s specific needs, financial capabilities, and operational priorities.
Understanding the types of fabrication shop software can frame the basis for making informed selections that directly impact efficiency and profitability.
Key Considerations for Selecting Fabrication Shop Software
Choosing the right fabrication shop software is crucial for enhancing productivity and efficiency within the manufacturing process. The right software can lead to better resource management, streamlined workflows, and ultimately, increased profitability. Given the variety of options available, organizations must consider specific elements that will best meet their needs. Key factors include scalability, user-friendliness, customer support, and pricing structures. Understanding these considerations will enable companies to surpass common pitfalls during the selection process and make informed decisions.
Scalability and Future Growth
Scalability is the ability of a system to grow with your business needs. When selecting fabrication shop software, it is crucial to consider whether the solution can adapt to your organization's future growth. As production demands increase, the software ought to scale without any loss in performance. Ideally, choose software that allows for adding features or expanding capabilities over time.
"Software that cannot evolve with your business can become a limitation, reducing the potential for efficiency and growth."
Investing in scalable software can prevent the need for additional costly replacements. Companies should assess their potential growth trajectory and select systems that meet those needs. Look for modular systems that let you add features as required.
Ease of Use and User Interface
The user interface of the software plays a significant role in its effectiveness. A complex interface can hinder productivity by creating confusion among staff. It is essential to choose software that offers a user-friendly design, encouraging quick adoption among employees. Simple navigation and intuitive design can minimize the time spent on training.
Conducting trials with different software options can provide insight into user experience. A straightforward interface can reduce the learning curve, allowing new users to become productive faster. Software that provides clear dashboards and reporting tools is often preferred.
Customer Support and Training Options
Effective customer support and training options are vital for successful software implementation. During the early stages, users are likely to encounter issues or have questions. Reliable customer support ensures these problems can be resolved rapidly. Check whether the software provider offers support through various channels like phone, email, or chat.
Additionally, comprehensive training sessions or educational resources can facilitate a smoother transition. Online tutorials, webinars, or in-person training sessions can be extremely beneficial. Make it a point to assess the level of support provided even after the initial rollout.
Cost and Pricing Models
Cost is always a critical factor when selecting software. Different software solutions come with varied pricing models. Organizations should clarify their budget and understand any fine print. Some vendors may require upfront costs, while others may offer subscription models. Consider who much ongoing maintenance or upgrade fees might affect overall expenses.
It's advisable to compare pricing from multiple vendors and request detailed breakdowns of what is included. Ensure that you are aware of the extent of features offered at each price point. Be cautious about attractions towards lower upfront costs while ignoring long-term financial implications.
Integration with Existing Systems
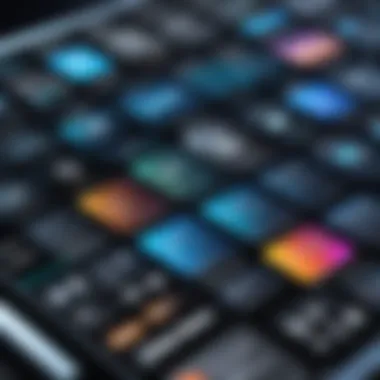
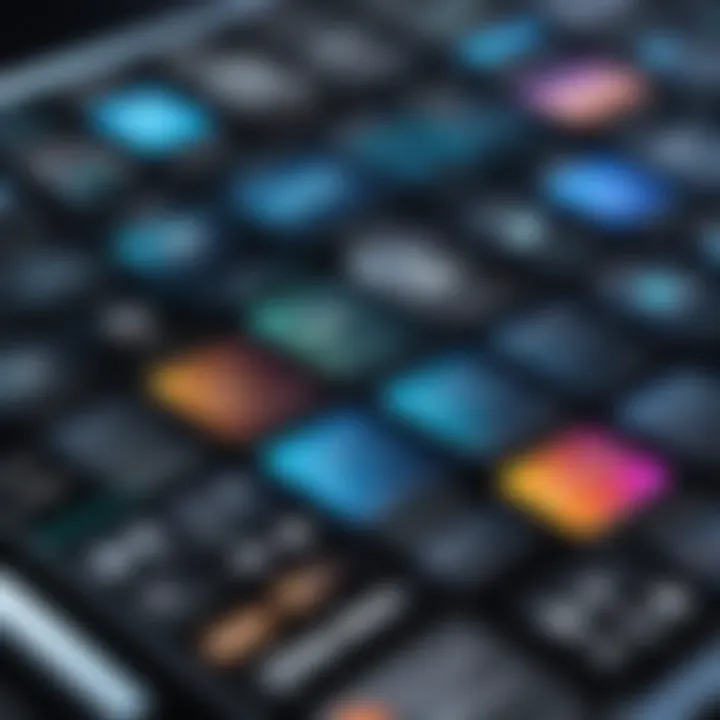
Integration with existing systems is a pivotal aspect when implementing fabrication shop software. As the sector becomes more reliant on technology for enhancing productivity, ensuring that new software can communicate seamlessly with pre-existing platforms becomes crucial. This integration not only fosters a unified operational environment but also reduces the chances of data silos, where information is trapped in one system and inaccessible to others.
Several key considerations arise when discussing integration. Firstly, it ensures data consistency across various departments, minimizing the risk of human error in data entry. This is particularly important in a fabrication shop where precise measurements and specifications are essential. When all systems are interconnected, a single source of truth is created, meaning that all stakeholders can rely on the same data for decision-making.
Second, integration boosts operational efficiency. By automating data transfer processes between systems like ERP, CRM, and accounting software, employees can focus on their core tasks rather than spending time manually transferring information. This efficiency translates directly into increased productivity within the shop.
Additionally, businesses can leverage analytics across integrated platforms for better insights into their operations. Having a consolidated view allows for effective data analysis, which can uncover trends and areas for improvement.
"Integration with existing systems leads to greater operational visibility and enhances decision-making capabilities across fabrication shops."
In summary, paying careful attention to the integration capabilities of fabrication shop software can lead to vastly improved workflows and decision-making processes, ultimately resulting in enhanced performance and profitability.
ERP Integration
Integrating fabrication shop software with Enterprise Resource Planning (ERP) systems is often one of the first steps taken when organizations look to improve their operational efficiency. ERP systems are designed to manage a wide array of business processes and including fabrication shop software within this ecosystem enhances coordination between departments.
By linking fabrication processes with ERP solutions, companies can gain real-time insights into inventory levels, production schedules, and resource allocation. This connectivity enables managers to make informed decisions swiftly, leading to operational agility. Moreover, recognizing potential delays or material shortages becomes easier, allowing for proactive measures rather than reactive ones.
Furthermore, ERP integration helps in maintaining compliance with industry standards by ensuring that all relevant quality control data is stored and managed within a single framework. This alignment fosters accountability and thorough documentation essential for audits and inspections.
CRM Integration
Integrating Customer Relationship Management (CRM) software with fabrication shop systems is another critical step that allows for better customer engagement and improved service delivery. A CRM system enables businesses to track customer interactions and manage sales processes effectively.
When fabrication shop software is integrated with CRM, companies can personalize their service by having access to relevant customer data. This includes order histories, preferences, and feedback. Understanding the customer journey can help in tailoring solutions that meet specific client needs.
Additionally, sales teams can benefit from real-time access to production capabilities. If a customer inquires about specific customization options, the sales representative can quickly verify the feasibility based on current workloads and production schedules.
Accounting Software Integration
Integrating accounting software with fabrication shop software ensures that financial data is consistently updated in real-time as operational data changes. With this integration, real-time revenue tracking becomes possible, allowing finance departments to monitor cash flow more effectively.
This integration also allows for a seamless transition of data between production outputs and financial reports. Errors in invoice generation can be reduced significantly, as the data used for billing will come directly from the fabrication shop system—decreasing the possibility of discrepancies.
Moreover, having accurate job costing information at one's fingertips enables better decision-making for bid evaluations and project profitability assessments. It contributes to clearer financial forecasting based on actual production metrics.
Customization and Flexibility
Customization and flexibility in fabrication shop software are crucial for adapting the system to suit unique business requirements. Each shop has its own processes, customer base, and material types. Therefore, a one-size-fits-all approach often leads to inefficiencies. The ability to customize features, workflows, and user settings ensures that the software aligns well with the shop's operational dynamics.
A flexible software solution allows businesses to make necessary adjustments without extensive reprogramming or investments. This adaptability can lead to increased user satisfaction and better operational outcomes because the software becomes a tool that complements existing practices rather than a disruptive force.
Customizable Features
The need for customizable features is paramount in maintaining relevant functionality. Fabrication shops utilize various methodologies and strategies in their processes. Customizable features may include tailored dashboards, specific data entry fields, and adjustable reporting formats. This ensures that users only access the information that's pertinent to their tasks, enhancing efficiency.
By allowing users to alter aspects like user permissions and visibility of data, fabrication shop software can cater to diverse roles within the organization. For instance, a shop floor manager might require a different set of tools and data analytics compared to a project estimator. The aim should be to provide all involved parties with options to configure their interfaces to their working styles and needs.
"Customization can significantly reduce time spent on task execution, leading to greater overall productivity."
These customizable features not only improve immediate user experience but also grow with the business. As new products or processes are introduced, the software can evolve alongside them, ensuring that adaptability is preserved.
User Configuration Options
User configuration options are another critical aspect of flexibility in fabrication shop software. Each user’s interaction with the software can be tailored. This means that different team members can set up their parameters to optimize performance.
Consider a scenario where an estimator frequently uses specific calculations. The ability to configure shortcuts or macros can save valuable time. This user-centric design approach empowers individuals to enhance their work processes while allowing the overall system to maintain coherence.
Moreover, user configuration options facilitate better training and onboarding. When new employees can personalize their learning experience, they tend to engage more deeply with the system. Consequently, they become productive sooner, which directly impacts the shop’s efficiency.
In summary, customization and flexibility in fabrication shop software are not merely conveniences; they are essential components that enable shops to thrive in competitive environments. As the industry continues to evolve, the call for more tailored solutions will only increase, highlighting the need for shops to consider these elements seriously in their software options.
Industry-Specific Applications
Understanding fabrication shop software requires looking at how it fits within specific industries. Each fabrication sector has unique challenges and processes that influence the key features needed in software solutions. By addressing the requirements of metal fabrication, woodworking shops, and plastic fabrication, businesses can enhance their operations effectively.
Metal Fabrication
Metal fabrication involves creating metal structures and components through cutting, bending, and assembling. Fabrication software for this industry focuses heavily on accuracy and efficiency. Tools like CAD (Computer-Aided Design) integration are vital. These tools allow engineers to create detailed models. It reduces errors in the manufacturing process, which can be costly.
Key benefits of metal fabrication software include:
- Improved precision: With advanced cutting tools, shops can achieve better accuracy.
- Streamlined workflows: The software automates many steps from design to production, minimizing manual input.
- Inventory management: Real-time tracking of materials ensures that projects stay on budget and schedule.
Woodworking Shops
In woodworking, the software needs to address both planning and execution aspects of projects. Woodworking shops deal with a variety of materials and designs. Therefore, flexibility in software capabilities is essential. Functionality for creating templates and managing complex inventory is invaluable.
The importance of tailored software for woodworking includes:
- Customization options: Users can craft specifications for various types of wood and projects with ease.
- Project management: Keeping track of multiple jobs is simplified. This can boost overall productivity.
- Design capabilities: Software that includes design tools allows for better visualization before production begins.
Plastic Fabrication
Plastic fabrication involves cutting, shaping, and molding plastics into desired designs. Software in this realm often emphasizes flexibility and adaptability. With different types of plastics used across applications, the software must accommodate various manufacturing processes such as injection molding or blow molding.
Key features beneficial for plastic fabrication software:
- Process simulation: This feature aids in understanding how the material will react during the fabrication process.
- Material management: Effective tracking of different plastic types and their characteristics ensures optimal usage amid varying projects.
- Collaboration tools: Helps in ensuring all team members are on the same page, especially in larger projects.
Each industry within fabrication has distinct needs. Understanding these differences is crucial for choosing the right software implementation.
By examining industry-specific applications, businesses can leverage technology effectively to improve their operations and enhance their market position.
Current Trends in Fabrication Shop Software
The landscape of fabrication shop software is constantly evolving. As industries seek higher efficiencies and greater profitability, staying updated on current trends is essential for decision-makers. Understanding these trends helps businesses make informed strategic choices. The intersection of automation, artificial intelligence, and data analytics is shaping how fabrication shops operate. Being cognizant of these elements can provide a competitive edge.
Emphasis on Automation
Automation in fabrication shops is not just a luxury; it has become a necessity. With the rising demand for faster production rates, automation tools are now at the forefront. They reduce labor costs and minimize human error.
- Benefits of Automation
- Increased Production Speed: Automated processes allow for quicker turnaround times on projects.
- Consistency: Machines maintain high quality throughout production without fatigue.
- Cost Reduction: With less manual intervention, operational costs drop significantly.

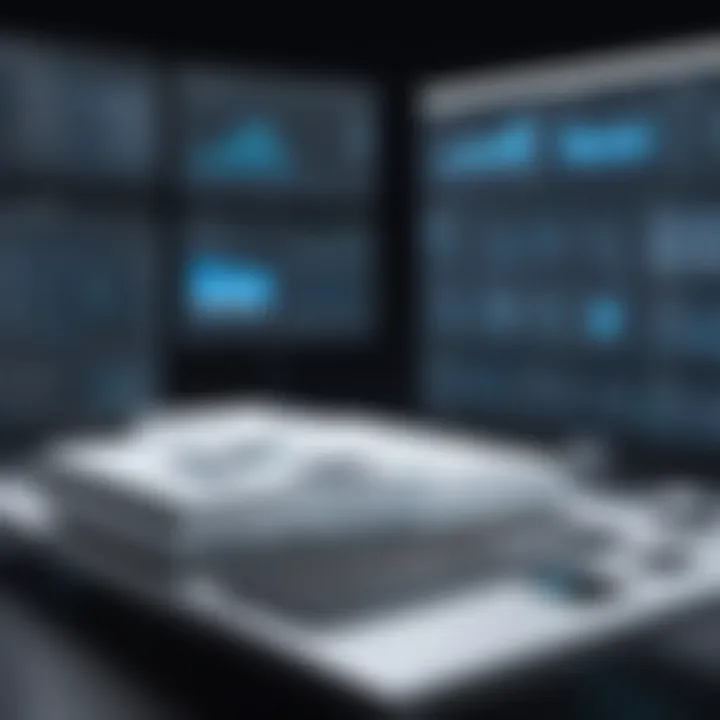
Automation also lends itself to real-time monitoring. Companies can track progress and adjust on the fly. This flexibility accommodates the varying demands of custom orders.
Artificial Intelligence Integration
Artificial intelligence is reshaping how shops operate. Integrating AI into fabrication software enhances decision-making. AI tools sift through vast amounts of data to provide predictive analytics.
- Predictive Maintenance: AI can foresee equipment failures before they occur, minimizing downtime.
- Optimization: Intelligent algorithms optimize resource allocation, ensuring maximum efficiency.
AI also facilitates better customer interactions. Chatbots and AI-driven platforms can manage inquiries, providing instant responses and improving customer satisfaction. The combination of speed and accuracy solidifies a business's reputation.
Data Analytics and Business Intelligence
Data analytics is crucial for fabrication shops. The ability to analyze data informs strategic decisions. Shops can track key performance indicators (KPIs) to assess their operations comprehensively.
- Key Data Metrics
- Production Efficiency: Understanding output levels can highlight areas for improvement.
- Cost Analysis: Data can uncover hidden costs, allowing for better budgeting.
- Customer Insights: Analyzing customer behavior aids in tailoring services to meet market demands.
Investing in robust data analytics platforms leads to improved overall performance. Business intelligence tools provide actionable insights, allowing for responsive operational adjustments.
"In today’s marketplace, the ability to quickly adapt and make data-driven decisions can determine a company’s success or failure."
In summary, keeping abreast of current trends in fabrication shop software is vital. Automation, AI, and data analytics are indispensable tools for maximizing efficiency and profitability. Ignoring these elements may result in missed opportunities in an increasingly competitive landscape.
Case Studies: Successful Implementation
The analysis of real-world applications of fabrication shop software offers valuable insights into its effectiveness. Examining case studies reveals how businesses can leverage software to address specific operational challenges and optimize performance. These examples provide tangible benefits and highlight critical factors necessary for successful software implementation. Understanding these dynamic processes can illuminate the path for other shops seeking to enhance their operations.
Company A: Increasing Efficiency
Company A specializes in metal fabrication and faced issues such as prolonged project timelines and high operational costs. Implementing fabrication shop software provided a structured approach to job management, enabling real-time tracking of project statuses.
The software's comprehensive dashboard allowed managers to view critical data at a glance. They could monitor labor hours, material usage, and machine availability in one unified platform. This integration reduced the time spent on manual reporting by approximately 30%. Additionally, automation tools simplified the quoting process, enabling quick responses to customer inquiries. The result was a significant decrease in lead times and an improvement in client satisfaction.
"Investing in strong software tools gave us the ability to see where efficiencies could improve and made informed decisions faster than ever," a project manager at Company A stated.
Notably, training programs were also crucial. Staff received tailored training sessions to familiarize them with the system's functions. This investment in human resource capacity contributed to a quicker adoption of the software, thus reinforcing overall effectiveness.
Company B: Streamlining Operations
Company B operates a woodworking shop and was dealing with inventory issues and chaotic scheduling processes. Before implementing fabrication shop software, the company frequently experienced stock shortages and overbooked resources, impacting their ability to meet customer demands on time.
With the new software, they could manage their inventory more strategically. The integrated inventory management feature allowed for real-time tracking of materials, ensuring that stock levels were adequate for upcoming projects. This capability led to a 40% reduction in times when materials ran low, drastically minimizing project delays.
Furthermore, the scheduling tools helped optimize resource allocation, aligning machine times to project timelines effectively. Managers used the scheduling module to visualize workload across teams, allowing for better planning and a significant decrease in downtime. Revamping their operational strategies with this software not only streamlined workflows but also improved overall productivity by 25%.
In summary, both companies demonstrated how proper implementation and training of fabrication shop software led to substantial operational improvements. By using these examples, other fabrication shops can glean insights on adaptable strategies tailored to unique needs. Choosing the right software can streamline operations, ultimately enhancing efficiency and profitability.
Challenges in Fabrication Shop Software Adoption
Adopting fabrication shop software presents a range of challenges that can hinder its successful implementation. Recognizing these challenges is vital for businesses aiming to improve their operational efficiency through technology. Understanding the potential pitfalls can help mitigate risks and ensure that the transition to new software is smooth and beneficial.
Resistance to Change
One significant challenge is the resistance to change. Employees may hesitate to embrace new software due to comfort with existing processes. This reluctance can stem from a fear of the unknown or concerns about their ability to learn the new system. It is crucial for management to recognize this resistance and address it proactively.
To combat this issue, organizations should invest time in training sessions. These sessions should illustrate not just how to use the software but also its benefits for daily tasks. By highlighting how the software streamlines work processes, employees may begin to see it as a valuable tool rather than an inconvenience.
Technical Difficulties
Another common hurdle is technical difficulties. Implementing new software often involves complex configurations, data migrations, and integrations with existing systems. Businesses may face challenges like software bugs, compatibility issues, or inadequate hardware. These technical problems can result in frustration among staff and may even cause delays in production.
To minimize these issues, organizations should conduct a thorough assessment of their current technical environment before adoption. Proper planning and testing can help identify potential problems early on. Engaging with software vendors for support during the installation phase can also lead to smoother transitions, ensuring that technical difficulties are resolved promptly.
Ongoing Maintenance Costs
Finally, ongoing maintenance costs are an essential consideration. After the initial adoption, maintaining the software requires continuous investment. This includes regular updates, IT support, and potential training for new features that may be introduced over time.
Companies must budget accordingly to avoid surprises. An unexpected increase in maintenance expenses can strain resources, undermining the software's intended benefits. Clear communication regarding costs, as well as setting aside funds for unforeseen expenses, can enhance readiness for the long-term commitments involved.
"The most successful implementations of fabrication shop software are those where challenges are anticipated and proactively managed."
In summary, while the adoption of fabrication shop software can transform a business's operations, it is not without its challenges. Resistance to change, technical difficulties, and ongoing maintenance costs represent key considerations that management must navigate to realize the full potential of their investment in technology.
Future Outlook for Fabrication Shop Software
The future of fabrication shop software is not just a matter of tools. It reflects broader trends in technology and manufacturing. Understanding this outlook is crucial for any business aiming to remain competitive and efficient in a rapidly changing environment.
Emerging Technologies
Emerging technologies such as the Internet of Things (IoT), machine learning, and advanced robotics are reshaping fabrication processes. IoT devices collect real-time data from machines, providing insights into operational efficiency and enabling predictive maintenance. This increases uptime and reduces costly downtimes.
Machine learning algorithms are also playing a significant role. They analyze historical data to improve forecasting for job management and inventory control. Tools such as Autodesk Fusion 360 and SolidWorks are incorporating these technologies, allowing shops to optimize designs and manufacturing processes seamlessly.
Moreover, augmented reality (AR) is becoming an essential tool for training and maintenance in fabrication shops. AR applications provide interactive guides, helping staff understand complex machinery operations without extensive manuals. As these technologies mature, they will lead towards smarter, more automated fabrication environments, making it easier for businesses to scale operations.
Predicted Market Trends
Market trends indicate a shift towards integrated systems that provide a comprehensive suite of tools within one platform. Companies are looking for solutions that offer not only job tracking but also inventory management and financial reporting in a single interface. This integration minimizes manual data entry and errors, streamlining processes.
Additionally, the rise of cloud-based solutions is notable. Companies prefer cloud systems for their flexibility and scalability. They allow for remote access, making it easy for teams to collaborate and monitor operations from anywhere. This trend is particularly appealing to smaller companies or startups that may lack the resources for costly on-premise infrastructure.
The demand for customization is also expected to increase. Fabrication shops often have unique needs depending on their specific industry focus, whether that's metal, wood, or plastic fabrication. Software that allows for tailored solutions will likely see more adoption as businesses seek to maximize their investment.
In summary, the future outlook for fabrication shop software is filled with innovations that promise to enhance productivity and efficiency. Being aware of these emerging technologies and market trends enables firms to prepare and adapt, ensuring they remain relevant in an evolving landscape.
"The integration of technology and fabrication processes will define the next decade in manufacturing."
It's essential for decision-makers and industry leaders to stay informed and proactive to leverage these advancements effectively.
The End
The conclusion serves as a pivotal element in this article, encapsulating the critical insights presented throughout. A well-rounded understanding of fabrication shop software is essential for modern manufacturing environments. This software not only streamlines processes but also significantly improves efficiency, accuracy, and overall productivity. By synthesizing the various features, benefits, and practical implications covered in the earlier sections, businesses can better grasp how to effectively integrate these tools into their operations.
Recap of Key Points
- Importance of Fabrication Shop Software: It plays a vital role in automating and optimizing tasks, helping shops operate more efficiently in competitive markets.
- Core Features: The software includes job tracking, inventory management, and resource allocation, which directly impact the day-to-day operations.
- Types of Software: Different solutions, like standalone systems or integrated solutions, meet diverse organizational needs.
- Integration Capabilities: The ability to seamlessly connect with existing systems such as ERP or CRM software enhances operational fluidity and data accuracy.
- Customization Options: Tailored features allow shops to adapt the software to fit their unique workflows and processes.
- Industry-Specific Applications: Each fabrication sector, be it metal or woodworking, often requires specific functionalities that must be addressed by the chosen software solution.
Final Thoughts on Fabrication Shop Software
Ultimately, adopting fabrication shop software goes beyond merely choosing a tool; it encompasses a strategic investment in the future of an organization. The evolving demands of the industry necessitate agile solutions that not only support current processes but also anticipate future growth. By integrating modern technologies such as artificial intelligence and data analytics, businesses can enhance decision-making abilities and gain a competitive edge.
"Investing in proper software today is not just a choice; it’s a necessity for long-term sustainability and growth within fabrications shops."