Job Shop ERP Systems: A Comprehensive Overview
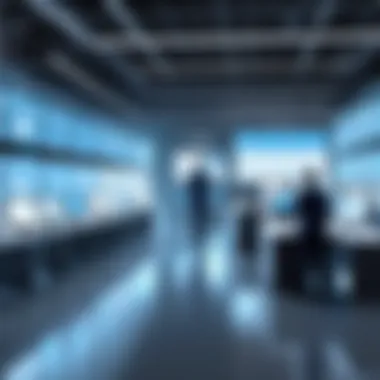

Intro
Enterprise Resource Planning (ERP) systems have become vital tools for businesses aiming to improve efficiency and streamline operations. Job shop ERP systems, in particular, cater to the unique requirements of manufacturing environments that deal with custom orders and varying production schedules. This article provides an in-depth exploration into the complexities of job shop ERP solutions, highlighting their functionalities, benefits, and selection strategies. With a focus on both small and medium-sized enterprises as well as larger corporations, readers will gain insights into how these systems can optimize their operational frameworks.
Key Features
Job shop ERP systems come equipped with distinct features that are crucial for managing complex production processes. These systems not only unify multiple aspects of manufacturing but also enhance overall visibility and control.
Overview of Core Features
The core features that define job shop ERP systems include:
- Work Order Management: Facilitates the creation, tracking, and management of work orders, ensuring timely completion and resource allocation.
- Inventory Management: Provides real-time monitoring of stock levels, helping avoid shortages and excess inventory.
- Scheduling Tools: Optimizes production schedules based on current workload and resource availability, enabling more efficient use of time and equipment.
- Cost Tracking: Monitors costs associated with materials, labor, and overhead, aiding in budget management and profitability analysis.
These features are essential for job shops because they must frequently adapt to unique customer requests and production challenges.
User Interface and Experience
The user interface of a job shop ERP should be intuitive and user-friendly. A well-designed interface can significantly reduce training time and improve staff adoption. Essential aspects of user experience include:
- Dashboard Customization: Users should be able to customize dashboards for quick access to relevant metrics and data.
- Mobile Accessibility: With an increase in remote work, mobile-friendly interfaces allow employees to access the system from various devices, ensuring flexibility.
- Data Visualization Tools: Graphical representations of data help in understanding complex information quickly and assist in decision-making.
A smooth user experience ensures that teams spend less time navigating the system and more time focusing on their core production tasks.
Pricing and Plans
When exploring job shop ERP systems, the pricing model is a crucial consideration. Many solutions offer flexible pricing structures to accommodate various business sizes and budgets.
Overview of Pricing Models
Pricing models typically include:
- Subscription-Based: This model allows businesses to pay a recurring fee for access to the software, often lower upfront costs.
- One-Time Purchase: Some vendors offer a one-time purchase option for the software, which may include additional costs for updates and support.
- Pay-Per-User: This flexible model allows firms to scale their costs based on the number of users accessing the system.
Comparison of Different Plans
Different ERP providers may offer a range of plans, with each providing distinct functionalities or levels of access. Businesses should evaluate:
- Availability of Features: Does a lower-tier plan meet your basic needs? Or will more advanced features be necessary?
- Support and Maintenance: Higher-tier plans may come with enhanced support options. Check what level of customer service is included.
- Trial Options: Some providers allow free trial periods. Testing the software can be instrumental in understanding fit for your operations.
Investing in the right job shop ERP system is not just about immediate costs; itโs about long-term operational efficiency and growth.
Preamble to Job Shop ERP
Understanding Job Shop ERP (Enterprise Resource Planning) systems is essential for manufacturers aiming to optimize their operations. These systems bridge various functions within a manufacturing business, ensuring seamless coordination among diverse teams and processes. The integration of these systems not only boosts productivity but also enhances the overall efficiency of job shops, particularly those that handle custom orders or small batch productions.
Definition of Job Shop ERP
Job Shop ERP refers to the suite of software tools designed specifically for manufacturers who operate in a job shop environment. A job shop typically focuses on producing custom products in varying quantities, as opposed to mass production. The ERP systems encompass modules that assist in scheduling, inventory management, order processing, and financial tracking, among other crucial operations. This system enables manufacturers to manage their resources efficiently, track job progress in real time, and respond swiftly to customer demands.
Importance of ERP in Job Shops
Implementing an ERP system in a job shop setting is increasingly viewed as a strategic necessity. Here are several key reasons that underscore its importance:
- Streamlined Operations: Job Shop ERP systems facilitate the integration of critical business functions. This leads to reduced redundancies and improved workflow.
- Enhanced Accuracy: With real-time data tracking, manufacturers can minimize errors in order fulfillment and inventory management. This accuracy translates into better customer satisfaction.
- Informed Decision-Making: Decision-makers can access comprehensive data analytics, enabling them to make well-informed choices that align with business goals.
- Scalability: As a job shop grows, its needs evolve. ERP systems can adapt to these changes, providing necessary resources and support.
Overall, ERP systems empower job shops to leverage technology for operational excellence. This focus on efficiency and effectiveness is critical for staying competitive in an ever-evolving manufacturing landscape.
"An ERP system is not just about managing resources; it's about transforming the way a job shop operates and delivers value to its customers."
For further reading on ERP systems, you can visit Wikipedia.
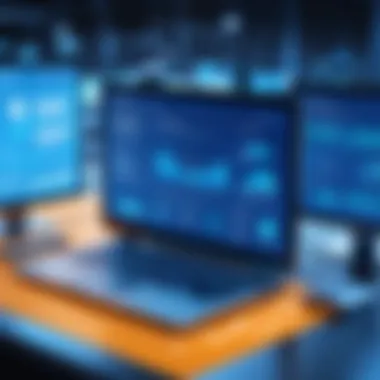

Key Features of Job Shop ERP Systems
In the context of job shop manufacturing, the features incorporated within an ERP system are pivotal for addressing the unique challenges faced by these environments. These key features not only streamline processes but also enhance operational performance. The effectiveness of any job shop ERP system lies in how well it can adapt to the specific needs of a job shop, thus making the understanding of its features essential.
Customization Capabilities
A primary feature of any job shop ERP system is its customization capabilities. Many job shops undergo constant change, adapting quickly to varying client demands and production schedules. A flexible ERP system can be tailored to meet unique operational requirements. This means businesses can modify workflows, forms, and reports to reflect their individual processes. With such adaptability, organizations can ensure that their ERP solution evolves with their specific needs and growth.
Customization can also extend to user interfaces, allowing businesses to configure dashboards and functionalities based on user roles. This personalization ensures that employees access relevant information faster, improving productivity and satisfaction.
Real-Time Data Tracking
The ability to track data in real time is fundamental for effective decision-making in job shops. This feature enables teams to monitor production statuses, resource utilization, and overall performance metrics continuously. Immediate access to this data can significantly reduce delays and enhance responsiveness to any arising issues.
Real-time data tracking provides insights into bottlenecks or irregularities in production. This kind of transparency not only leads to proactive problem resolution but also informs future planning, helping businesses optimize processes further. A system that provides real-time analytics can transform data into actionable intelligence, which is invaluable in a competitive landscape.
Resource Management
Resource management is another crucial feature of job shop ERP systems. Efficiently managing resources, including materials, labor, and machinery, is key to maintaining profitability in a job shop setting. An effective ERP solution can help track inventory levels, manage supply chains, and allocate labor resources appropriately.
This capability assists decision-makers in ensuring they have the right materials at the right time, thus minimizing wastage and ensuring timely deliveries. Moreover, proper resource management contributes to cost control, financial planning, and informs strategic decisions regarding capacity and workforce.
"The right job shop ERP system can significantly alter the operational landscape, making it essential for businesses to choose wisely."
These features are not just enhancements; they are fundamental to optimizing the entire workflow within a job shop.
Benefits of Implementing Job Shop ERP
Job shop ERP systems offer significant advantages that can drastically improve operational dynamics within manufacturing environments. The benefits not only impact the internal processes but also extend to customer interactions and financial outcomes. Understanding these advantages is crucial for businesses looking to maximize the potential of their ERP implementation.
Improved Efficiency
One of the primary benefits of implementing a job shop ERP is improved efficiency across multiple facets of operation. By centralizing information and automating routine tasks, these systems facilitate streamlined workflows. For instance, real-time data tracking allows shops to monitor production stages, enabling immediate adjustments when delays or issues arise. This agility reduces downtime and enhances productivity.
Furthermore, integrating processes such as inventory management and scheduling through ERP minimizes manual tasks. Employees can focus on high-value activities rather than administrative chores. This optimization fosters an environment where resources can be allocated effectively, ultimately leading to increased throughput.
Efficient processes in job shops can directly translate to quicker turnaround times for clients, solidifying the companyโs reliability in the market.
Cost Reduction
Cost considerations are paramount in any business, and job shop ERP systems contribute significantly to reducing unnecessary expenses. By providing comprehensive visibility into all operational areas, these systems enable better control of resources and budgeting. For example, ERP helps identify waste in production, such as excess material use or inefficient labor allocation.
Moreover, accurate forecasting capabilities within ERP assist companies in better planning their sourcing and production cycles. This leads to reduced inventory costs, as businesses can minimize excess stock while ensuring production meets demand. With lower operational costs, organizations can enhance their profit margins, making job shop ERP a financially sound investment.
Enhanced Customer Satisfaction
In today's competitive landscape, customer satisfaction can be a key differentiator. Job shop ERP systems enhance this area by ensuring that manufacturers can meet their clients' needs effectively. With improved efficiency and reduced lead times, businesses are more equipped to deliver on time, enhancing trust with customers.
Additionally, these systems enable better communication and transparency throughout the order process. Clients can receive updates on their orders in real-time, significantly increasing the likelihood of positive interactions. When customers feel informed and valued, their loyalty towards the company strengthens, further contributing to long-term success.
Challenges in Job Shop ERP Implementation
Implementing Job Shop ERP systems comes with distinct challenges that need careful consideration. In this section, we will explore these challenges in detail. Addressing these issues is vital for ensuring a successful ERP deployment. Understanding these hurdles allows businesses to prepare adequately and strategize their approach effectively.
Data Migration Issues
Data migration stands as a prominent challenge when transitioning to an ERP system. This process involves transferring existing data from legacy systems to the new ERP platform. Often, the data can be inconsistent, poorly structured, or even outdated.
The significance of data accuracy cannot be overstated. It directly affects the ERP's ability to provide reliable insights and operational efficiency. Companies may encounter problems as they attempt to cleanse, format, and validate data for the new system. Familiarity with both systems is required to ensure completeness in migration. In addition, a well-thought-out data migration plan should be created. This includes defining data requirements, creating mapping processes, and establishing testing protocols.
Resistance to Change
Another major challenge is resistance to change within the organization. Employees may be accustomed to existing processes and systems. Any shift to new ERP solutions may be met with skepticism. This resistance can stem from fear of the unknown or concerns about potential job loss.
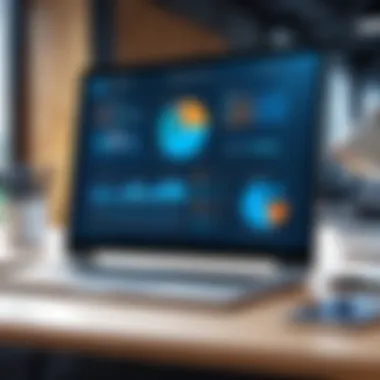

To address this, it is essential to foster a culture of openness and communication. Involvement of all levels of staff during the implementation phase can help ease fears and increase acceptance. Implementing training sessions tailored to different user groups helps also build confidence in the new system. Change management strategies must focus on demonstrating the benefits of ERP systems. Such benefits include improved workflow, better collaboration, and increased productivity.
Cost Considerations
Lastly, cost considerations are paramount for businesses contemplating ERP adoption. Implementing an ERP system involves various expenses, including software licensing, hardware updates, and consultant fees. Additionally, hidden costs may arise from unforeseen circumstances, such as extended training periods or technical support.
Budgeting realistically for these expenses is important. Businesses should conduct a thorough cost-benefit analysis to understand potential returns on their investment. It is crucial that decision-makers evaluate the long-term savings an efficient ERP system can provide against initial expenditures. By doing so, firms can make informed decisions that stay aligned with economic goals.
Effective foresight on these economic factors is integral to successful ERP implementation.
In summary, challenges in Job Shop ERP implementation encompass data migration issues, resistance to change, and cost considerations. Each of these challenges requires attentive strategies and a proactive approach. Addressing these difficulties can pave the way for a more seamless transition to a new ERP system, ultimately enhancing operational efficiency and business success.
Best Practices for Job Shop ERP Selection
Selecting the right ERP for a job shop is critical. A wrong choice can lead to inefficiencies and increased costs. Therefore, following best practices during this process is essential. Business needs must be assessed properly, vendor solutions evaluated, and a thorough cost-benefit analysis conducted. Each of these elements contributes to making an informed and effective decision that aligns with company objectives. Here are detailed steps to guide the selection process.
Assessing Business Needs
Understanding the unique characteristics of one's job shop is the first step. This involves identifying the specific challenges and goals of the business. Consider the following:
- Capacity Requirements: What are the production needs? Understand the maximum capacity and how it fluctuates.
- Work Order Management: How will the system improve current work order processes? This includes tracking tasks from start to finish.
- Integration Needs: Does the business use other software, such as CAD or inventory management? Determine the compatibility of the ERP system with existing tools.
- User Roles: Identify who will use the system and their technical proficiency. Training may be necessary based on skill levels.
Once these needs are clear, it is easier to identify which features are vital for the ERP system.
Evaluating Vendor Solutions
With a list of needs in hand, the next step is to evaluate potential vendor solutions. Several key aspects to consider include:
- Reputation: Research the vendor's history. Long-standing companies often provide reliability.
- Customization Options: Assess how well the system can be tailored to the unique processes of the shop.
- Support Services: Is there a strong customer support team? Consider vendors who provide training sessions and ongoing support.
- Scalability: As the business grows, will the ERP system grow too? Look for solutions that can evolve with the company.
Take time to read reviews and testimonials from current or past users. This can provide insights into common issues faced.
Conducting a Cost-Benefit Analysis
Finally, a comprehensive cost-benefit analysis is crucial. This analysis should detail the expected returns from the investment in ERP systems compared to the actual costs. Elements to include:
- Implementation Costs: Factor in both direct and indirect costs associated with the setup.
- Training Expenses: Ensure to account for the workforce training needed for effective ERP use.
- Maintenance Fees: Acknowledge ongoing costs that might arise post-implementation.
- Expected Benefits: Identify specific metrics, like time savings or reduced waste.
A thorough cost-benefit analysis ensures that decision-makers can justify the investment based on tangible metrics.
Utilizing these best practices enhances the chances of selecting an ERP system that genuinely improves efficiency and effectiveness within a job shop environment. Companies are more likely to avoid common pitfalls by thoroughly assessing needs, scrutinizing vendors, and analyzing costs against benefits.
Integration with Existing Systems
Integrating job shop ERP systems with existing operations is essential for maximizing functionality and ensuring efficiency. This integration is not merely about connecting software; it involves aligning the ERP with a variety of operational processes, thus allowing data sharing and communication between platforms. Key benefits include enhanced data accuracy, streamlined workflows, and a holistic view of operations. Organizations must approach this task with careful consideration of the systems currently in use and the intended outcomes of the integration.
Interfacing with Manufacturing Systems
Effective interfacing between job shop ERP systems and manufacturing systems is crucial for several reasons. Firstly, it allows for real-time data exchange, which promotes informed decision-making. When a job shop's ERP is connected to manufacturing execution systems (MES), production schedules, inventory levels, and machinery efficiency can be monitored and adjusted on the fly. This interface helps in minimizing downtime and maximizing resource utilization.
Moreover, compatibility with manufacturing systems facilitates better tracking of work orders and production processes. Job status updates can be fed directly into the ERP, which keeps all stakeholders aware of progress. The integration creates an environment where data silos are eliminated.
"Real-time data flow is the backbone of effective job shop management."
To achieve a seamless interface, organizations can utilize application programming interfaces (APIs) or middleware. These tools act as bridges, enabling different systems to communicate effectively. When selecting an ERP, companies should prioritize vendors that offer robust integration capabilities with current manufacturing systems.
Compatibility with Accounting Software
The compatibility of job shop ERP systems with accounting software is another critical aspect. Financial data plays a vital role in business operations, and ensuring that this data flows smoothly between systems can significantly improve financial management processes.
Linking the ERP to accounting software allows for automatic updates of financial records based on real-time operational data. This reduces human errors that often accompany manual data entry and provides a transparent financial overview. Additionally, the integration aids in budget tracking, cost management, and forecasting.
Another benefit is the consolidation of reports. When the ERP and accounting software work in tandem, creating comprehensive financial statements becomes less complicated. Businesses can derive insights into profitability, cash flow, and overall financial health with greater ease.
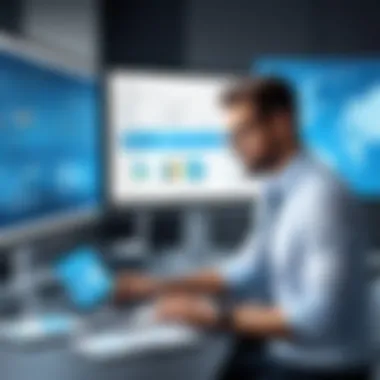

It is crucial to select ERP solutions that are designed to work with widely used accounting software such as QuickBooks, Xero, or SAP. Compatibility considerations should be a top priority during the selection process.
Integrating job shop ERP systems with existing manufacturing and accounting systems is not a trivial task but presents considerable potential rewards. Organizations that navigate this process effectively will likely see substantial improvements in operational efficiency and financial clarity.
The Future of Job Shop ERP Systems
The evolution of job shop ERP systems is marked by continuous advancements in technology and changing market demands. Understanding the future of these systems is critical as it can shape the way manufacturers streamline their operations. Adapting to new trends and technologies ensures that businesses maintain a competitive edge while maximizing productivity. Additionally, a clear eye on the future allows organizations to prepare for potential challenges in the dynamic manufacturing sector.
Trends in ERP Technology
As technology evolves, job shop ERP systems are not left behind. Key trends are shaping the landscape of ERP technology, making it essential for manufacturers to stay informed. Here are some notable trends:
- Cloud-Based Solutions: The shift towards cloud computing is significant. Cloud-based ERP systems offer flexibility, scalability, and accessibility, allowing businesses to operate from anywhere. This trend reduces the need for extensive on-site IT infrastructure.
- Mobile Access: With the rise of mobile technology, job shop ERP systems are increasingly designed to be accessible via smartphones and tablets. This mobile access enables immediate updates and access to critical data, improving decision-making processes.
- Integration of IoT: The Internet of Things (IoT) integration into ERP systems allows for enhanced data collection and analysis. By connecting machines and devices, manufacturers can track performance metrics in real-time, optimizing processes and maintenance.
- Data Analytics: Modern ERP solutions emphasize powerful data analytics features. Businesses can leverage data insights informed by their operations to identify trends, reduce costs, and enhance decision-making.
- User Experience Enhancements: As the need for intuitive interfaces increases, ERP vendors are focusing on enhancing the user experience. Improved interfaces lead to higher usage rates and better integration across departments.
These trends highlight the direction in which job shop ERP systems are headed and the possibilities they hold for improving efficiency in manufacturing.
Impact of Artificial Intelligence
Artificial intelligence is a transformative force in many industries, and job shop ERP systems are no exception. The integration of AI into ERP systems can significantly improve operational efficiency. Below are ways AI is affecting the future of job shop ERP:
- Predictive Analytics: AI can analyze historical data and trends to predict future outcomes. This capability allows manufacturers to anticipate demand, optimize inventory levels, and make informed decisions about production schedules.
- Automation of Routine Tasks: AI technology can automate repetitive tasks, freeing up employees to focus on more complex and value-adding activities. This automation can lead to significant labor savings and reduced human error.
- Smart Recommendations: AI can provide actionable insights based on analyzed data. For example, it can suggest optimal production sequences to minimize downtime and increase throughput.
- Enhanced Customer Service: AI-driven chatbots can manage customer inquiries efficiently. This leads to faster response times and higher customer satisfaction.
"The implementation of AI in job shop ERP systems not only enhances functional efficiency but also fosters a more agile manufacturing environment."
In summary, keeping an eye on these advancements is vital for organizations that want to leverage the full potential of job shop ERP systems. Awareness of trends and the impact of AI will ensure that businesses are prepared to adapt and thrive in evolving market conditions.
Case Studies: Successful ERP Implementations
Examining real-world examples of successful ERP implementations in job shops provides invaluable insights into the practical benefits and challenges associated with these systems. Case studies serve as a powerful tool for understanding not only what is possible but also what is necessary to achieve desired outcomes in operational efficiency and cost savings. By analyzing how specific companies have leveraged job shop ERP systems, decision-makers can identify patterns, strategies, and potential pitfalls that may influence their ERP journey.
Case studies highlight critical elements, such as implementation timelines, user adoption challenges, and the measurable impacts of ERP on business processes. These narratives often demonstrate how tailored solutions can address unique production demands, ultimately leading to improved workflows and sustainable growth. Through these examples, the article aims to emphasize that the success of an ERP system often hinges on careful planning and execution.
"Real-world examples can be more illustrative than theoretical discussions, providing concrete evidence of benefits gained from ERP adoption in the field."
Company A: Efficiency Gains
Company A, a medium-sized job shop specializing in custom metal fabrication, faced increasing pressure to improve their production throughput while maintaining quality. Prior to implementing an ERP system, they struggled with manual scheduling, resulting in frequent delays and miscommunications.
Upon integrating a robust job shop ERP system tailored to their needs, Company A experienced substantial improvements in efficiency. Key features such as real-time data tracking and resource management allowed them to optimize their production schedule effectively. With the newly implemented system, production managers could monitor job statuses and resource availability in real time, minimizing idle time and bottlenecks.
The most notable outcome was a 30% increase in overall labor efficiency within the first six months of implementation. Additionally, the automation of repetitive tasks freed employees to focus on more value-adding activities, significantly enhancing workplace morale. The clear visibility of operations provided by the ERP system fostered better communication between departments and led to fewer errors, ultimately improving customer satisfaction with faster turnaround times.
Company B: Cost Saving Strategies
Company B, a specialized manufacturer of electronic components, found itself grappling with rising operational costs and an outdated production process. The introduction of a job shop ERP system was aimed at identifying cost-saving opportunities while still delivering high-quality products.
The organization used the ERP system to perform a comprehensive cost-benefit analysis of different production methods. By identifying the most cost-effective resources and processes, they managed to cut down waste and reduce production costs by 25%. The system facilitated demand forecasting, which allowed Company B to optimize inventory levels. This ensured they were not overstocking or understocking critical components.
Additionally, the analytics provided by the ERP platform helped in negotiating better terms with suppliers, leading to long-term savings. As a result, Company B reported a significant improvement in their bottom line by not only reducing costs but also enhancing productivity by reallocating resources more effectively.
Closure
The conclusion serves a vital role in penetrating the depths of the discourse presented throughout this article. It encapsulates the significance of Job Shop ERP systems in the modern manufacturing landscape. As manufacturers continue to navigate complex operational challenges, the role of ERP becomes increasingly indispensable. The insights offered in the previous sections, inclusive of features, benefits, and integration strategies, provide a clear view of how these systems contribute to operational efficiency and business growth.
Summary of Insights
The journey through this article has highlighted several critical elements of Job Shop ERP systems. Some of the key takeaways include:
- Customization: Job Shop ERP systems offer robust customization capabilities, allowing businesses to tailor functionalities to their unique needs.
- Efficiency Gains: Implementing an ERP system can predicate substantial improvements in efficiency and productivity.
- Data-Driven Decisions: The availability of real-time data enables informed decision-making, a crucial aspect in todayโs competitive market.
- Future Relevance: With ongoing trends such as AI integration, the relevance of ERP systems is expected to grow, transforming manufacturing operations.
In summary, understanding these components provides a comprehensive perspective on the multifaceted role of ERP systems in job shops.
Final Recommendations
To harness the full potential of Job Shop ERP systems, organizations must consider several recommendations:
- Conduct a Thorough Needs Assessment: Before selecting an ERP solution, it is essential to evaluate specific business needs and challenges.
- Choose a Scalable Solution: Opt for an ERP system that can grow with your business, adapting to future needs without significant overhauls.
- Invest in Training: Ensure employees are adequately trained in the new system to minimize resistance and enhance adoption rates.
- Monitor After Implementation: Establish robust monitoring practices to assess efficiency gains and areas for further improvement.
These steps can ensure that the transition to a Job Shop ERP system not only meets immediate operational goals but also supports long-term strategic objectives.