Comprehensive Examples of Inventory Systems

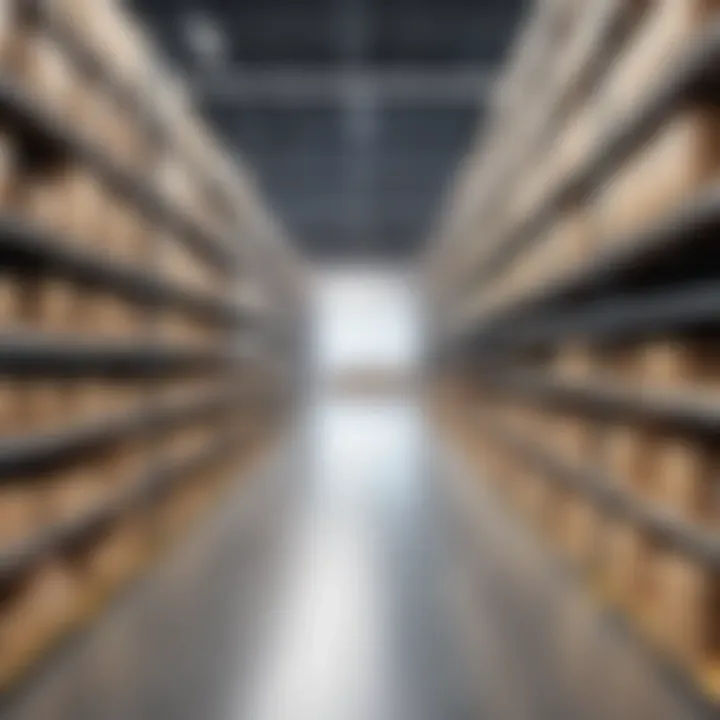
Intro
Inventory management is a crucial component in the operations of any business. Having the right inventory system can significantly impact efficiency, cost-control and overall business performance. This article seeks to illuminate the complex landscape of inventory systems by showcasing various examples and dissecting their functionality.
An effective inventory system helps organizations manage stock levels, track order fulfillment, and ensure that the right products are available at the right time. Today's automated solutions vary widely across industries, adapting to different needs and challenges. As we delve into these examples, readers will find insights that are invaluable for making informed decisions regarding inventory management.
Key Features
Overview of Core Features
Inventory systems typically offer a range of core features designed to streamline operations. Essential functionalities include:
- Real-Time Tracking: Systems provide real-time visibility into inventory levels, helping businesses understand what items are in stock and where they are located.
- Order Management: Automated processes for receiving, fulfilling, and shipping orders can significantly enhance efficiency.
- Reporting and Analytics: Advanced reporting capabilities allow businesses to analyze sales trends, forecast demand, and make strategic decisions.
- Integration: Compatibility with other business systems, such as accounting software or e-commerce platforms, is vital for cohesive operations.
These features can enhance productivity and reduce errors.
User Interface and Experience
A user-friendly interface can significantly impact how effectively an inventory system is utilized. Many solutions are designed with intuitive dashboards that present users with essential data at a glance. Key aspects of user experience include:
- Ease of Navigation: Users should be able to find features quickly without extensive training.
- Customizable Views: Flexibility in displaying inventory data allows users to focus on what matters most to them.
- Mobile Access: In today's world, mobile compatibility is crucial. This feature allows users to manage inventory on-the-go.
Having a seamless user experience is not just about aesthetics. It directly influences productivity and reduces training time.
Pricing and Plans
Overview of Pricing Models
When selecting an inventory system, understanding the pricing model is essential. Solutions typically fall into various categories:
- Subscription-Based: Monthly or annual fees provide access to the software, inclusive of updates and support.
- One-Time Purchase: Some systems require a hefty upfront investment for perpetual licenses. Additional costs may arise for support and updates.
- Usage-Based: Payment is based on the volume of transactions or orders processed, offering flexibility for smaller businesses.
Choosing the right pricing model can affect cash flow and long-term sustainability.
Comparison of Different Plans
Many inventory systems offer tiered plans that cater to different business sizes or needs. For instance, a system like TradeGecko might offer basic features at a lower tier while providing robust options for enterprises requiring more complex functionalities. Key elements to consider in this comparison include:
- Feature Availability: Higher-tier plans often unlock advanced automation and reporting tools.
- User Limits: Some plans restrict the number of users, which could require companies to scale up their investment in the future.
- Customer Support: Higher-priced plans may offer enhanced support options, which can be crucial for troubleshooting.
Ultimately, businesses must assess their current and future needs to select a plan that aligns with their operational demands.
Foreword to Inventory Systems
An effective inventory system underpins the operational success of various businesses. It is not merely about keeping track of stock; it encompasses a comprehensive approach to managing resources, cashflow, and meeting customer demands. This article delves into inventory systems that cater to diverse sectors, highlighting their characteristics and relevance in today's dynamic market landscape.
Understanding inventory systems provides businesses with significant benefits. First, they enhance accuracy in tracking items, which minimizes losses and errors. Secondly, these systems promote efficiency, helping organizations to streamline operations, reduce holding costs, and optimize inventory levels. Lastly, informed decision-making relies heavily on real-time data, which effective inventory systems facilitate.
Definition and Importance of Inventory Systems
Inventory systems are structured methodologies used to keep track of products and materials in stock. They include various techniques and software solutions aimed at monitoring, managing, and optimizing inventory levels. The importance of these systems cannot be overstated: they serve as the backbone for managing supply chains, ensuring that a company can meet its customers' needs while maintaining operational efficiency.
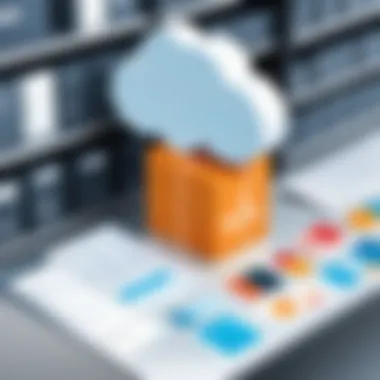
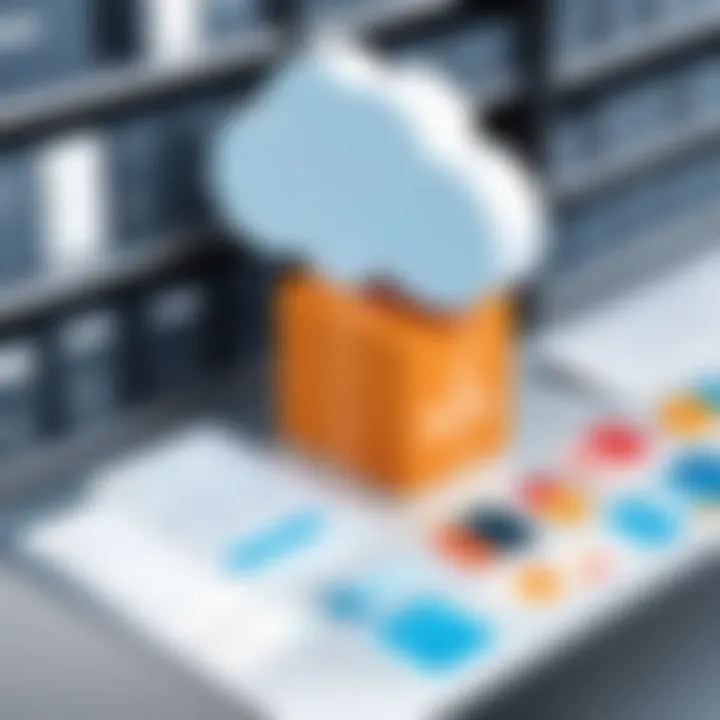
Proper inventory management contributes to better cash flow by minimizing excess stock and reducing carrying costs. Furthermore, it fosters improved customer satisfaction through timely deliveries and availability of products.
Challenges in Inventory Management
Despite the benefits, inventory management presents several challenges.
- Complexity: Many businesses deal with a variety of products, including different sizes, colors, and brands. The complexity increases as businesses scale.
- Inaccurate data: Relying on manual entry can lead to errors. Misinformation affects purchasing decisions and can lead to stockouts or overstocking.
- Cost management: Balancing inventory levels against operating costs is tricky. Holding too much inventory ties up precious resources, while too little can result in lost sales opportunities.
Addressing these challenges requires effective planning, resource allocation, and leveraging technology into inventory systems to streamline processes and enhance accuracy. Each inventory solution discussed in this article aims to mitigate such challenges, providing tailored approaches for distinct business environments.
"Effective inventory management is not just a technical operation; it's a strategic advantage that can differentiate a leading firm from its competition."
Understanding these concepts sets the stage for exploring the types of inventory systems available and their specific uses in various industries.
Types of Inventory Systems
Understanding the different types of inventory systems is essential for organizations seeking to improve management practices. Each system offers distinct benefits tailored to various operational needs. Choosing the correct type can significantly enhance efficiency, minimize costs, and improve service delivery. This section will examine the more common inventory systems, focusing on their specific features and the scenarios where they excel.
Periodic Inventory System
The periodic inventory system is one of the simplest forms of inventory management. In this approach, the inventory is not tracked on a daily basis. Instead, businesses conduct physical counts at specific intervals—often monthly, quarterly, or annually. The advantages of this system include relative low-cost implementation and simplicity of use.
However, it also has its downsides. For instance, knowing inventory levels only at scheduled intervals can lead to stockouts or overstocked items. Accuracy is a significant concern, as discrepancies can arise between actual inventory and recorded data. Businesses handling large volumes or fast-moving goods may find this system inadequate. Thus, while it may work well for smaller operations, larger businesses or those with high turnover might need a more robust solution.
Perpetual Inventory System
In contrast, the perpetual inventory system continuously tracks inventory levels in real time. Utilizing technology, businesses can update inventory records after each transaction—whether it's sales, purchases, or returns. This system is particularly beneficial for companies seeking immediate insights into stock levels.
The benefits include enhanced accuracy and improved ability to respond to changes in demand. Businesses can analyze sales data frequently to optimize stock levels and minimize wastage. However, implementing a perpetual system requires investment in technology and software solutions, which may not be feasible for every business. Many organizations opt for this method due to its adaptability to modern business needs.
Just-in-Time Inventory System
The just-in-time (JIT) inventory system focuses on reducing waste and improving efficiency by receiving goods only as they are needed in the production process. This system minimizes inventory costs by maintaining low stock levels and synchronizing deliveries with production schedules.
While JIT can significantly lower holding costs and optimize cash flow, it comes with inherent risks. A disruption in the supply chain can lead to production delays since there is little to no room for error in timing. Businesses must maintain strong relationships with suppliers to ensure reliability. Manufacturing in sectors such as automotive often employs JIT for its efficiency and skillful management of inventory.
ABC Inventory System
The ABC inventory system categorizes inventory into three classes to optimize management efforts. 'A' items are high-value but low-quantity; 'B' items are moderate in value and quantity, while 'C' items are low-value and high-quantity. This system allows companies to focus resources on managing 'A' items, which can significantly impact the bottom line.
One primary advantage of the ABC system is its efficient allocation of management effort. Rather than treating all items equally, businesses can prioritize based on value and criticality. However, implementing this system requires rigorous analysis of inventory data and may not be suitable for smaller businesses that lack diverse inventory lines. Companies let's say like Walmart could benefit greatly from it, allowing for focused oversight and control of their vast inventory.
Each of these inventory system types serves different business needs, illustrating the fundamental importance of understanding selection criteria based on organizational objectives and resources.
Warehouse Management Systems
Warehouse management systems (WMS) focus on the effective management of warehouse operations. They ensure the smooth handling, tracking, and storage of goods, which is crucial for any organization.
Key Features and Benefits
The key features of warehouse management systems include real-time tracking, automated inventory replenishment, and multi-user access. These features contribute to increased accuracy and efficiency. By providing real-time data, WMS helps in minimizing errors, which enhances overall productivity. Automated processes reduce the time taken for various operations, helping businesses manage inventory effectively.
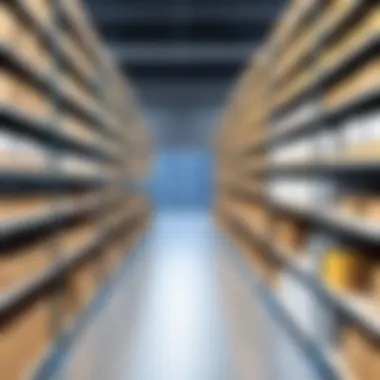
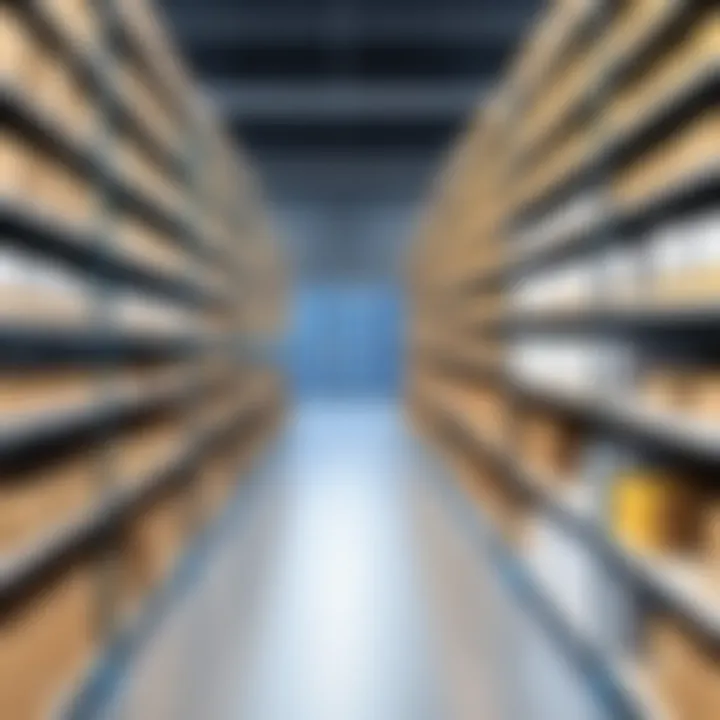
Popular Software Solutions
Several software solutions are available for warehouse management. SAP Extended Warehouse Management, Oracle Warehouse Management, and Fishbowl Warehouse are notable examples. Each provides unique functionalities that cater to specific needs. For instance, SAP Extended Warehouse Management offers strong integration capabilities. However, the choice of software can depend on the scale and nature of the warehousing operation.
Retail Inventory Systems
Retail inventory systems are designed to meet the specific needs of retail operations. Effective management of inventory in a retail environment is critical, given the constant flow of products.
Overview of Retail Inventory Needs
The overview of retail inventory needs showcases the necessity for accurate tracking of stock levels, sales forecasting, and supplier management. These elements are vital for maintaining optimal inventory levels and preventing stockouts or overstock situations. A well-organized retail system can respond quickly to changing customer demands, thus maximizing revenue potential.
Top Retail Software Examples
In the retail space, solutions like Shopify, Lightspeed, and Square have gained popularity. They provide essential features such as sales tracking and integration with e-commerce platforms. Such software allows retailers to manage their inventory seamlessly across multiple channels. Nevertheless, it's important to choose software based on specific business requirements and sales strategy.
Manufacturing Inventory Systems
Manufacturing inventory systems focus on maintaining adequate stock levels to support production processes without interruptions. These systems are crucial in ensuring that raw materials and finished products are properly managed.
Specific Requirements of Manufacturing
Specific requirements in manufacturing revolve around demand forecasting, lead time management, and the management of work-in-progress inventory. These aspects ensure a smooth manufacturing process and minimize production delays. Accurate inventory management leads to efficient use of resources and enhances product quality.
Leading Software in Manufacturing
Some leading software options in manufacturing include NetSuite, Fishbowl Manufacturing, and MRPeasy. They typically offer functionalities like production planning and real-time inventory tracking. Selection of the right software should consider the manufacturing process, size of operations, and growth trajectory of the company.
E-commerce Inventory Management
E-commerce inventory management deals with the unique challenges faced by online retailers in managing stock availability and order fulfillment.
Challenges Unique to E-commerce
The challenges unique to e-commerce often include handling returns, managing multiple sales channels, and inventory forecasting. These complexities require robust systems that can seamlessly track inventory across platforms. They allow businesses to meet customer expectations efficiently while maintaining control over stock levels.
Recommended E-commerce Inventory Solutions
For effective e-commerce inventory management, solutions such as TradeGecko, Zoho Inventory, and QuickBooks Commerce are highly recommended. These platforms offer integration with e-commerce sites and analytics tools for better decision making. While each solution has its benefits, businesses should evaluate their specific needs and budget constraints before making a choice.
Advantages and Disadvantages of Various Inventory Systems
Understanding the advantages and disadvantages of different inventory systems is crucial for businesses aiming to optimize their operations. Each system offers distinct benefits, but they also come with their own challenges. This section discusses the essential elements that influence the effectiveness of these systems in varied contexts. The insights shed light on considerations like cost efficiency, ease of use, accuracy, and adaptability to change. Making informed decisions based on these factors can significantly impact a company's overall performance.
Comparative Analysis of Inventory Systems
When evaluating inventory systems, several aspects must be discussed. Each system has its unique strengths that suit specific business needs. For example, periodic systems tend to be simpler and require less tech support. However, they may not provide real-time data, which can lead to stockouts or overstocking.
On the other hand, perpetual systems allow for continuous tracking of inventory levels, which enhances accuracy. Yet, they often come with higher initial costs due to the technology needed to implement them.
Let's examine some key comparisons:
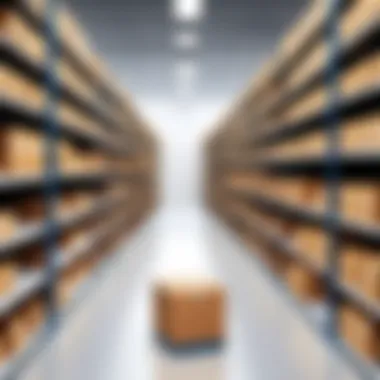
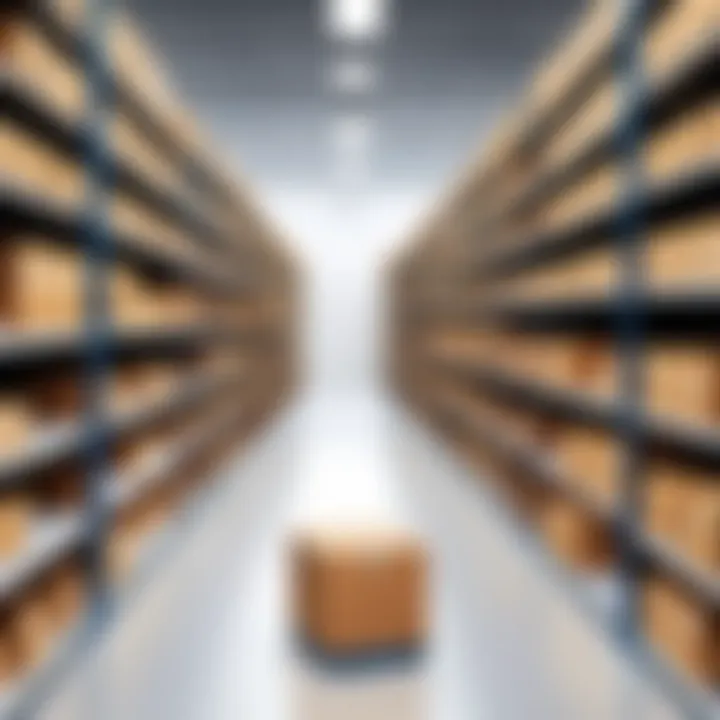
- Cost: Periodic systems generally involve lower costs but may miss discrepancies in inventory. Perpetual systems require higher investment but provide better tracking solutions.
- Data Accuracy: Traditional methods may lead to errors and inaccuracies, while modern systems align with real-time inventories.
- User-Friendliness: Some systems are easier to use than others, necessitating proper training and knowledge.
"Selecting the right inventory system requires understanding the unique needs of your business and the trade-offs associated with each option."
Trade-offs in System Selection
Selecting an inventory system involves various trade-offs. Each factor needs careful consideration. These include:
- Budget Constraints: Low-cost options may save money upfront but could lead to higher long-term costs due to inefficiencies.
- Business Size: A smaller business may benefit from simpler systems. Larger firms might need more complex solutions to handle higher volumes.
- Implementation Time: Some systems can be set up quickly, while others may require extensive training and time.
- Scalability: Systems that work well for small operations may not scale efficiently as the business grows.
- Integration with Other Systems: Often, businesses rely on varied software. Ensuring compatibility is essential to streamline operations.
Factors Influencing Inventory System Selection
Understanding the factors that influence the selection of an inventory system is critical for businesses seeking to optimize their inventory practices. The right system can enhance efficiency, reduce waste, and improve customer satisfaction. It is not merely about choosing a system; it is about aligning the system with the operational objectives of the business.
Several key elements affect the choice of inventory system, including the size and type of the business, as well as the industry standards it must comply with. Each factor offers unique considerations that can lead to significant disparities in operational efficacy.
Business Size and Type
The size and type of a business strongly dictate the inventory system that will be most effective. For small businesses, a straightforward system with less complexity may suffice. These companies often benefit from simpler methods like manual tracking or basic software. On the other hand, larger organizations require robust systems capable of handling high volumes of data and transactions.
- Small Business: Often lean and agile, these entities can utilize basic inventory processes to maintain control over stock without incurring high costs.
- Medium to Large Business: Typically needs complex systems such as Enterprise Resource Planning (ERP) solutions. These systems not only manage inventory but integrate financials, logistics, and other functions to ensure seamless operations.
The type of business also comes into play. Retail operations may prioritize real-time data to manage customer demand, whereas manufacturing may focus on material requirements planning to streamline the production process. Each sector has distinct needs that the inventory system should address.
Industry Standards and Requirements
Industry standards and legal requirements significantly influence inventory system selection. These can include specific regulatory compliance, reporting standards, and best practices unique to each field. Adhering to these standards is not an option; it is a necessity.
- Regulatory Compliance: Many industries, like pharmaceuticals or food and beverage, are highly regulated. Failing to adhere to inventory tracking and record-keeping standards can lead to severe consequences, including fines or legal repercussions.
- Best Practices: Certain industries have established best practices that guide how inventory is managed. For example, the retail sector often employs just-in-time methodologies to minimize stock on hand while meeting customer demand.
Choosing an inventory system that supports ongoing compliance and operational excellence can save businesses from unnecessary risks and improve overall performance.
In summary, the choice of inventory system is influenced by the specific characteristics of the business and the regulatory environment in which they operate. An awareness of these factors allows businesses to select the most suitable inventory management practices, ensuring not only compliance but also operational efficiency.
Ending
In the context of inventory systems, drawing insightful conclusions is vital. It encapsulates not only the critical elements discussed but also the overarching principles that guide effective inventory management. As businesses face fluctuating demands and supply chain complexities, understanding the core insights becomes essential in optimizing their operations.
Summary of Key Insights
Key insights include:
- Different systems offer tailored solutions based on industry requirements.
- The choice of inventory system directly impacts efficiency, cost, and customer satisfaction.
- Integration capabilities with existing business processes are crucial for seamless operation.
For example, Warehouse Management Systems come with features like real-time tracking and automated replenishment, enhancing performance significantly. In contrast, Retail Inventory Systems focus on inventory turnover and sales analytics to keep up with market trends.
These insights collectively serve as a roadmap for IT managers and business decision-makers to navigate the increasingly complex landscape of inventory management.
Future Trends in Inventory Systems
As we look ahead, several trends are likely to influence inventory management systems. Technology advancements will play a pivotal role in shaping inventory systems. Here are notable trends:
- Artificial Intelligence and Machine Learning: These technologies will enhance forecasting accuracy, allowing businesses to better anticipate demand changes.
- IoT Integration: The Internet of Things will facilitate real-time data collection, leading to more responsive inventory management strategies.
- Cloud-based Solutions: Ongoing migration to cloud systems will ensure greater accessibility and flexibility, improving collaboration across supply chains.
- Sustainability Focus: Companies are increasingly seeking eco-friendly solutions, prompting the development of greener inventory practices.
"The effectiveness of inventory management lies in its ability to adapt and integrate with advancing technologies."
Thus, staying informed about these trends is essential for professionals aiming to maintain competitive advantage. The ongoing evolution of inventory systems highlights the importance of adaptable strategies that can meet current and future business demands.