Exploring the Essentials of Work Order Programs
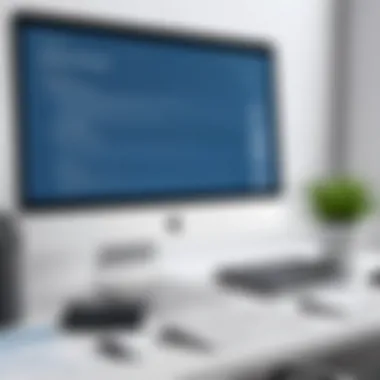
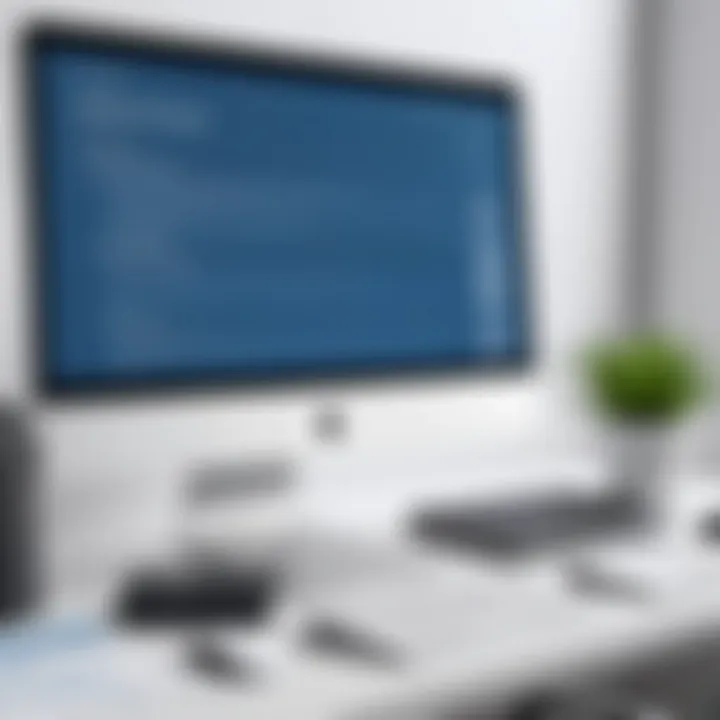
Intro
Understanding work order programs is crucial in today's fast-paced business environment. These systems play a significant role in streamlining operations, ensuring that tasks are organized and completed efficiently. Many organizations implement work order programs to enhance operational effectiveness and improve management of resources. The focus here will be on the foundational elements of these programs and their implications for workplace productivity.
Key Features
Overview of Core Features
Work order programs have various essential features that contribute to their utility in an organizational context. One core feature is task management, which allows teams to create, assign, and track tasks easily. This eliminates confusion and ensures everyone understands their responsibilities.
Another important aspect is report generation. This enables businesses to monitor progress and identify bottlenecks in workflows. By analyzing this data, companies can make informed decisions to enhance productivity. The integration of mobile access is also vital, allowing employees to access and update work orders in real time, regardless of their location.
User Interface and Experience
The user interface (UI) plays a pivotal role in the effectiveness of work order programs. A clean, intuitive UI helps users navigate the system quickly. This can reduce training time and increase adoption rates among staff. Features such as drag-and-drop functionalities and customizable dashboards enhance the overall user experience. In addition, feedback mechanisms, such as notifications and alerts, keep users engaged and informed about the status of tasks and projects.
Pricing and Plans
Overview of Pricing Models
When selecting a work order program, understanding the various pricing models is essential. Many software solutions operate on a subscription basis, with monthly or annual fees. This model allows for predictable budgeting, as businesses know their expenses upfront. Some platforms also offer tiered pricing, where additional features are provided at higher price points.
Comparison of Different Plans
To aid decision-making, it’s beneficial to compare plans from specific vendors. For instance, products like ServiceTitan and FMX cater to different niches, offering features that suit distinct operational needs. Below are key considerations for comparison:
- Features Offered: Analyze the features included in each plan, ensuring they align with your specific requirements.
- Scalability: Consider how well the software can grow with your business.
- Customer Support: Research the level of customer support offered, as this can be critical during implementation and daily use.
Effective implementation of work order programs results not only in immediate improvements in operational efficiency but also positions the organization for long-term success.
By exploring these key aspects of work order programs, organizations can gain clarity on how to choose and implement the right system that maximizes performance and fosters productivity.
Foreword to Work Order Programs
Understanding work order programs is crucial for organizations aiming to improve operational efficiency. These programs are a systematic approach to managing tasks and resources, ensuring that processes run smoothly and effectively. By integrating work order management into daily operations, businesses can enhance productivity and streamline workflows.
Definition and Purpose
A work order program serves as a centralized system for creating, tracking, and managing work orders. Essentially, a work order is a document that outlines tasks or requests requiring attention. The purpose of these programs extends beyond mere task management. They facilitate communication, ensure accountability, and provide valuable insights into resource allocation and project timelines.
Effective work order programs can lead to:
- Improved response times to requests
- Clear prioritization of tasks
- Enhanced tracking of work progress
Moreover, they play a significant role in maintaining records, which helps in future analyses and audits.
Historical Context
The inception of work order programs can be traced back to manual systems that utilized paper-based logs for task management. Initially emerging in manufacturing environments, these systems were basic and often prone to errors. As technology evolved, so did the complexity and efficiency of work order programs.
In the late 20th century, the introduction of computer-aided management systems transformed how work orders were processed. Organizations began adopting software solutions to automate workflows, resulting in significant time savings. Today, work order programs leverage cloud computing, mobile applications, and integration with enterprise resource planning (ERP) systems. This evolution reflects a broader trend towards digitization in business, making these programs indispensable in modern operations.
Core Components of Work Order Programs
The core components of work order programs form the fundamental structure necessary for their effective deployment and management. Understanding these components is crucial for organizations aiming to streamline operations and enhance overall productivity. These elements include different types of work orders, the lifecycle each order undergoes from inception to completion, and how well these systems integrate with existing operational frameworks.
Work Order Types
Work order types vary based on their specific purposes, and recognizing these distinctions is essential for tailoring processes to organizational needs. Common types include reactive work orders, which address unforeseen issues, and preventive work orders, intended for regular maintenance activities. Each type serves a unique role:
- Reactive Work Orders: Initiated by reported problems, these orders are crucial in minimizing downtime.
- Preventive Work Orders: Scheduled tasks that aim to prevent equipment failure through regular checks.
- Corrective Work Orders: Focused on fixing issues that have already occurred.
- Project Work Orders: Related to larger initiatives requiring multiple tasks to achieve specific outcomes.
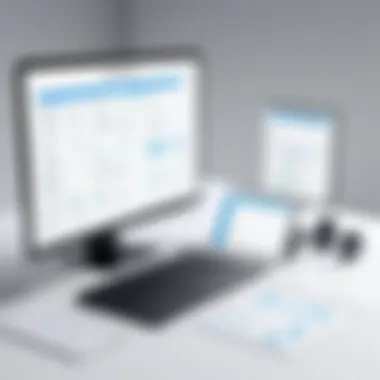
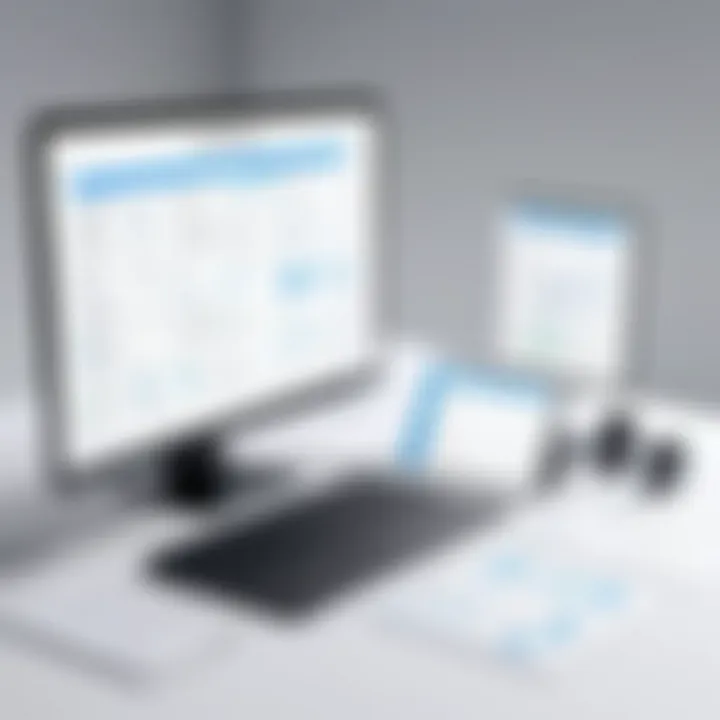
By categorizing work orders, managers can allocate resources efficiently, ensuring that urgent matters receive immediate attention while also having preventive measures in place.
Work Order Lifecycle
The lifecycle of a work order spans several stages, each critical for effective management and resolution. This lifecycle generally includes:
- Creation: The initiation of a work order, where details of the task are outlined.
- Approval: Review and authorization by relevant stakeholders.
- Assignment: Designating resources or personnel to carry out the task.
- Execution: The actual completion of the work as specified in the order.
- Closure: Finalizing the order once the task is completed and all necessary documentation is submitted.
A clear understanding of this lifecycle helps in minimizing delays and ensures accountability at each step. Managers can track performance metrics effectively, allowing for insights into operational efficiency.
Integration with Other Systems
Integration with other systems is vital for the seamless functioning of work order programs. Connecting work order systems to asset management, inventory control, and maintenance scheduling tools enhances data flow and decision-making.
Benefits of integration include:
- Improved Data Accuracy: Reduces discrepancies that can arise from manual entry.
- Enhanced Communication: Facilitates better information sharing across departments.
- Resource Optimization: Allows for dynamic resource allocation based on real-time data.
- Streamlined Processes: Reduces redundancies, making workflows more efficient.
By integrating work order software with existing systems, organizations can achieve a holistic view of operations, fostering an environment where data-driven decisions can significantly improve performance.
"Effective work order management is not just about tracking tasks; it's about creating a cohesive operational strategy."
The core components outlined above play a pivotal role in ensuring that work order programs are not only kept organized but also highly functional, adapting to the needs of different sectors while driving efficiency.
Applications of Work Order Programs
Work order programs have become essential in optimizing various operations within diverse sectors. Their implementation enhances efficiency, facilitates better resource allocation, and improves task management. Understanding the applications of work order programs is crucial for organizations aiming to streamline processes and drive productivity. This section delves into how these systems are utilized across different industries and the benefits they confer.
Manufacturing Sector
In the manufacturing sector, work order programs play a pivotal role in managing production processes. They allow organizations to issue and track production orders effectively. This capability ensures that materials and resources are allocated efficiently, minimizing downtime. A well-implemented work order management system can lead to shorter lead times and quicker response to market demands.
Key benefits in manufacturing include:
- Improved Inventory Management: Tracking raw materials and finished goods more accurately helps in reducing excess stock and shortages.
- Enhanced Quality Control: Work orders facilitate the documentation of production processes, which is vital for quality assurance and compliance with industry standards.
- Maintenance Scheduling: Regular maintenance can be planned through work orders, reducing unexpected breakdowns and increasing equipment lifespan.
Facility Management
In facility management, effective handling of maintenance requests is crucial. Work order programs enable facility managers to prioritize tasks based on urgency and importance. This functionality allows for more organized and timely maintenance, which contributes to operational safety and efficiency.
Key aspects of work order applications in facility management include:
- Responsive Service Delivery: Quick turnaround on maintenance requests improves tenant satisfaction in residential and commercial buildings.
- Tracking and Reporting: Facility managers can analyze trends in service requests, enabling them to manage resources proactively rather than reactively.
- Compliance and Safety: Ensuring that maintenance is performed regularly helps in adhering to safety regulations, thereby minimizing potential risks.
Field Services
Work order programs are integral to field service operations. They help in managing the tasks of technicians as they perform repairs and installations on-site. Organizations can schedule and dispatch workers more effectively, which increases service efficiency.
Key benefits of work order systems in field services include:
- Real-Time Updates: Technicians can access work orders remotely, allowing them to receive updates and changes instantly while in the field.
- Customer Communication: Enhanced communication platforms integrated with work order management enable better engagement with clients about service status and expectations.
- Resource Optimization: Allocating the right technician for the right task reduces costs and increases job completion rates.
IT and Software Management
In IT and software management, work order programs streamline support ticketing and IT maintenance schedules. These programs assist in maintaining software updates, managing hardware requests, and solving technical issues efficiently.
Key considerations for IT applications include:
- Priority Handling: Work orders can categorize issues by severity, ensuring critical problems are addressed promptly, which is vital in IT environments.
- Tracking Asset Lifecycle: IT departments can manage hardware and software lifecycles effectively through systematic orders, helping anticipate needs for upgrades or replacements.
- Integration with ITSM Tools: Work order systems can often integrate with IT Service Management (ITSM) tools, further enhancing the management of technical resources and support services.
Work order programs significantly enhance operational efficiency by ensuring that tasks are prioritized, monitored, and completed timely across various sectors.
Selecting Work Order Software
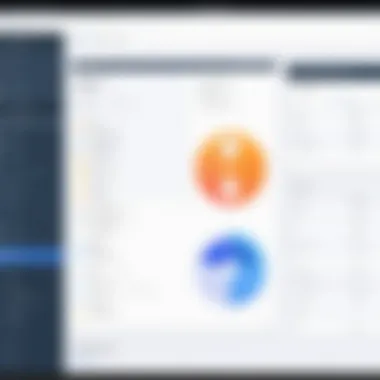
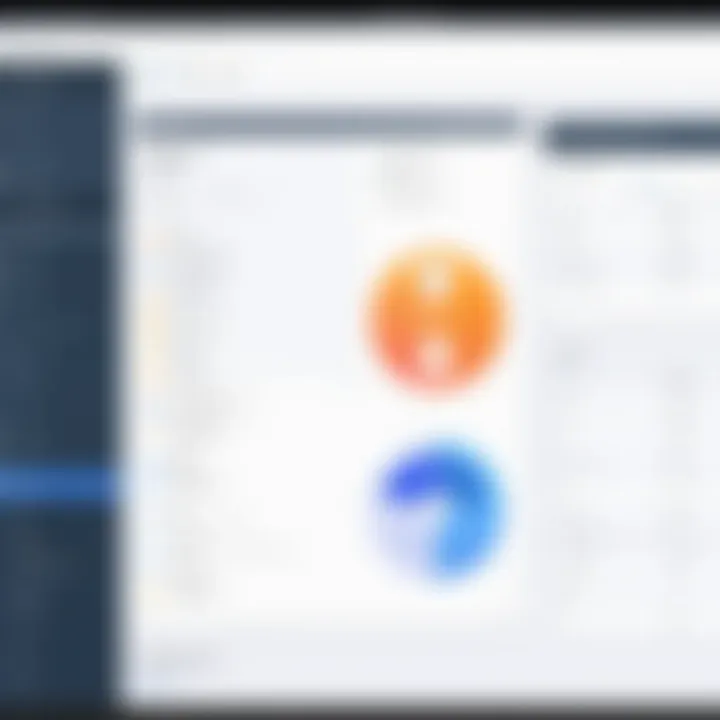
Choosing suitable work order software is a critical step in maximizing operational efficiency. The right software can streamline work order management processes, enhance communication among teams, and significantly boost productivity. When selecting software, organizations must evaluate not only the functionalities offered but also how these align with specific business needs. Proper software selection can lead to improved tracking of work orders, quicker response times, and better resource management.
Key Features to Consider
When evaluating work order software, several key features must be considered:
- User-Friendly Interface: A software with an intuitive design allows users from various backgrounds to navigate easily and utilize its features without extensive training.
- Customization Options: The ability to adapt the software according to specific workflows and processes is essential. Customizable fields and forms allow organizations to tailor the solution to fit their unique requirements.
- Integration Capabilities: It is crucial that the software can integrate seamlessly with existing systems such as customer relationship management (CRM) or enterprise resource planning (ERP) tools to ensure data consistency and streamline operations.
- Mobile Access: Given the nature of many work environments, having mobile capabilities ensures that field workers can access and update work orders on the go.
- Reporting and Analytics: Robust reporting tools can provide insights into work order performance, allowing for data-driven decision-making and identifying areas for improvement.
Vendor Evaluation Criteria
Selecting the right vendor is as important as choosing the software itself. Certain criteria can help in evaluating potential vendors:
- Reputation: Look for vendors with a strong track record and positive reviews. Feedback from current users can reveal strengths and weaknesses.
- Customer Support: Adequate support services should be readily available. Good vendors should provide easy-to-reach customer service and extensive documentation to aid users.
- Implementation Support: Evaluate the vendor's resources for assisting with implementation. Proper guidance during setup can significantly affect how smoothly the transition occurs.
- Future Scalability: Choose a vendor whose software can grow with your organization. Consider if the vendor can support scaling services and whether they have a roadmap for future innovations.
- Costs: Take into account all associated costs, not just purchase price. Ensure that maintenance, support, and upgrade fees fit within the budget.
Cost Considerations
Cost is a major factor when selecting work order software. Organizations need to consider various cost aspects:
- Initial Investment: Assess the upfront costs, which include software purchase or subscription fees. Compare pricing models to identify the most cost-effective option.
- Operating Costs: Consider the ongoing operating costs, including licensing fees, maintenance, and support. A clear understanding of these costs can help manage the budget effectively.
- Hidden Costs: Be attentive to potential hidden costs, such as training expenses or costs associated with the integration into existing systems.
- Return on Investment (ROI): Evaluate potential ROI by assessing how the software could save time and resources. Improved efficiency can justify the investment made.
Organizations must conduct thorough research and prepare a comprehensive analysis of their needs when investing in work order software. The benefits gained can far outweigh the investment if the right solution is chosen.
Implementation Strategies
Implementing effective work order programs is pivotal for businesses aiming to maximize operational efficiency. Strategies must be meticulously planned and executed. Without a well-thought-out approach, organizations may encounter obstacles that impede successful implementation. Here, we will detail significant elements for successful deployment, the benefits achieved through these strategies, and key considerations that must not be overlooked.
Project Planning and Execution
A strong foundation in project planning is essential for any work order program. The planning phase includes defining scope, goals, timelines, and resources needed. In this context, it is vital to involve all relevant stakeholders to ensure that every aspect of the organization’s needs is captured. A comprehensive project plan should outline specific roles and responsibilities, which fosters accountability.
Steps include:
- Identifying Requirements: Clearly articulate what your work order system should achieve.
- Selecting Tools: Choose the right software that aligns with organizational goals.
- Resource Allocation: Ensure adequate manpower, time, and financial resources are allocated for execution.
Execution must follow established timelines. Regular monitoring of progress against the plan ensures that deviations are managed promptly. Integration of agile methodologies can further enhance adaptability throughout the execution phase.
Training and User Adoption
Training is often underestimated but is crucial for the success of work order programs. User adoption directly influences system efficacy. Investing in training ensures that users are proficient and comfortable with the new processes.
Training programs should be customized based on user roles and their interaction with the software. For instance, front-line workers may require practical, hands-on training, whereas managerial staff might benefit more from theoretical workshops.
Benefits of a well-structured training program include:
- Increased user confidence in using the system.
- Reduction in errors due to lack of knowledge.
- Higher productivity levels as users become more efficient in utilizing the program.
Adoption challenges can arise; thus, ongoing support is necessary. Create channels for feedback that encourage users to voice concerns and suggest improvements.
Data Migration Challenges
Data migration is a complicated yet essential element in implementing work order systems. Moving existing data into a new system poses several challenges. These might include data loss, corruption, or incompatibility issues.
Prior to data migration, conducting a thorough audit of existing data is important. Identify what data is necessary and what can be discarded. Clean and normalize the data to ensure it meets required standards before transfer.
Here are some key points to consider during data migration:
- Data Mapping: Ensure all fields in the old system align with the new system.
- Testing: Perform test migrations to identify any potential issues ahead of full-scale transfer.
- Backup: Always maintain a backup of data before initiating migration, allowing for recovery if problems occur.
Best Practices in Managing Work Orders
Managing work orders effectively is crucial in maintaining operational efficiency within any organization. The implementation of best practices can streamline processes, reduce operational risks, and improve service delivery. Focusing on these practices allows businesses to leverage their resources efficiently, ensuring tasks are completed on time and within budget.
Regular Audit and Review
Conducting regular audits and reviews of work orders is essential for identifying bottlenecks and inefficiencies. These audits help the team understand how resources are allocated and whether they are being used optimally. There are several benefits of implementing a systematic review process:
- Identifying Inefficiencies: Audits reveal patterns that may indicate where work orders are delayed or where resources are not being utilized correctly.
- Adjusting Processes: Review sessions allow teams to discuss findings and adjust workflows or processes accordingly, fostering continuous improvement.
- Enhancing Compliance: Regular reviews help ensure that the organization adheres to industry standards and regulatory requirements, reducing the risk of non-compliance.
This ongoing process of evaluation promotes accountability within teams and ensures that all personnel involved in managing work orders are aligned with the organization’s goals.
Utilizing Analytics for Improvement
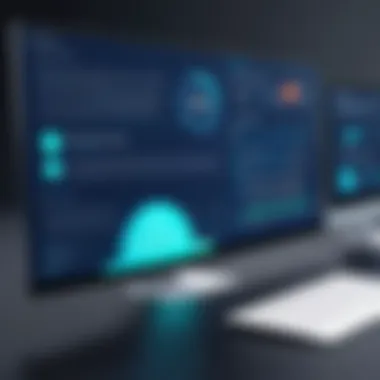
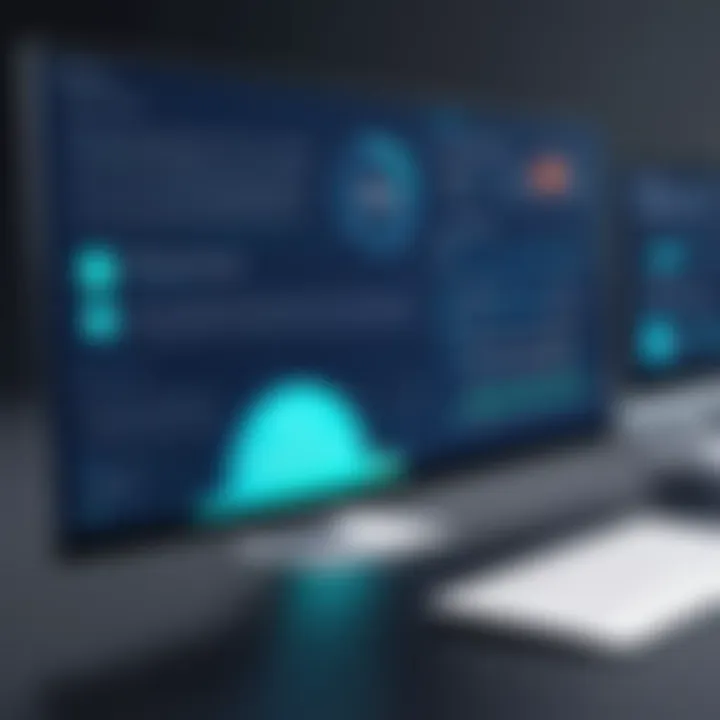
Analytics plays a vital role in managing work orders effectively. By collecting and analyzing data, organizations can make informed decisions about their work order processes. Incorporating analytics into the management strategy provides several key advantages:
- Data-Driven Decisions: Using analytics enables decision-makers to rely on factual information rather than intuition.
- Performance Metrics: Key performance indicators can be tracked to assess the efficiency and effectiveness of work orders over time.
- Predictive Insights: Advanced analytics can identify trends, helping forecast demand for maintenance or repairs before issues arise.
Businesses can use various tools that integrate analytics capabilities, ensuring they have comprehensive visibility over their processes and outcomes.
Feedback Mechanisms
Incorporating feedback mechanisms into work order management is vital for continuous improvement. Feedback from different stakeholders, including employees, vendors, and clients, helps identify areas for improvement. Here’s how effective feedback mechanisms can enhance work order management:
- Employee Input: Engaging employees in the feedback process allows them to voice their experiences and suggestions, leading to better practices and morale.
- Customer Satisfaction: Feedback from customers can highlight problems or shortcomings in service delivery, providing valuable insights into areas needing attention.
- Iterative Improvements: By regularly collecting and analyzing feedback, organizations can implement changes iteratively, ensuring ongoing alignment with stakeholder expectations.
Establishing an effective feedback system fosters a culture of transparency and accountability, leading to improved performance in managing work orders.
"Regular audits, effective use of analytics, and a robust feedback culture are key drivers to ensure effective work order management."
Implementing these best practices in managing work orders is not merely a checklist but a commitment to continuous improvement and operational excellence. It sets the stage for companies to adapt in a rapidly changing business environment.
Future Trends in Work Order Management
The landscape of work order management is transforming rapidly. As organizations strive for efficiencies, several trends emerge that shape the future of these programs. Understanding these trends is essential for decision-makers to align their strategies effectively. Key trends include the influence of artificial intelligence (AI) and automation, growth of mobile technologies, and increased focus on sustainability. These factors will alter how businesses operate and how work orders are managed.
Impact of AI and Automation
AI and automation are revolutionizing work order management. Automation reduces manual tasks, enabling teams to focus on higher-value activities. With AI integration, systems can predict maintenance needs and prioritize work based on urgency.
The benefits are vast:
- Increased Efficiency: Automation streamlines operations, reducing processing time.
- Data-Driven Decisions: AI analyzes historical data, helping predict future needs.
- Enhanced Accuracy: Automated systems minimize human error in data entry and task assignment.
However, there are considerations when implementing these technologies. Organizations must ensure workforce readiness for these changes. Engage in training programs to familiarize staff with new tools.
Mobile Technologies
The adoption of mobile technologies is increasingly vital in work order management. Employees now access work orders and relevant tools on their mobile devices, regardless of their location. This transition to mobile provides significant advantages:
- Real-Time Updates: Field personnel receive immediate notifications of changes to work orders, enhancing responsiveness.
- Improved Communication: Teams can collaborate more effectively through instant messaging or status updates on mobile platforms.
- Increased Flexibility: Employees can manage tasks on-the-go, increasing productivity.
This shift does come with challenges. Organizations need to invest in secure mobile apps and ensure they are user-friendly. Security protocols must also be in place to protect sensitive data.
Sustainability Considerations
Sustainability is becoming a fundamental aspect of business operations, including work order programs. Companies are increasingly required to adopt sustainable practices, which involves reevaluating how work orders are handled. Key considerations include:
- Resource Optimization: Efficient use of resources reduces waste and lowering costs.
- Environmental Impact: Sustainable work orders can help track and minimize the ecological footprint of operations.
- Corporate Responsibility: Consumers and investors prefer companies that demonstrate a commitment to sustainable practices.
Incorporating sustainability into work order management strategies can lead to long-term benefits. Organizations should regularly assess the sustainability of their processes and aim for certification where possible.
Culmination
The conclusion section serves as a pivotal element in this article, synthesizing the comprehensive exploration of work order programs. It not only encapsulates the critical points discussed but also emphasizes the significance of these programs in enhancing operational efficiency for businesses.
Summary of Key Points
Throughout the article, several essential aspects of work order programs have been highlighted:
- Definition and Purpose: Work order programs serve to streamline maintenance and service requests, making it essential for organizations aiming for efficiency in operations.
- Core Components: The varied types of work orders, their life cycles, and how they integrate with other systems were discussed, outlining their interconnectedness.
- Applications Across Sectors: The versatility of work order programs is clear, with applications spanning manufacturing, IT, and facility management.
- Selecting Software: Key features, evaluation criteria for vendors, and considerations related to cost were detailed to assist decision-makers in choosing the right software solutions for their specific needs.
- Implementation Strategies: Effective planning, training, and addressing data migration challenges are critical to ensure smooth integration of work order programs into an organization.
- Best Practices: Regular audits, leveraging analytics, and implementing feedback mechanisms were established as best practices for management.
- Future Trends: The impact of AI, mobile technologies, and sustainability were examined as growing trends shaping the future of work order management.
These points present a clear framework for understanding work order programs, pointing to their vital role in improving efficiency and productivity in various sectors.
Final Thoughts on Adoption
Adopting a robust work order program is not merely a technological shift; it is a strategic decision that can transform how an organization operates. Embracing this change requires an open-minded approach to new systems and processes.
By implementing these programs, organizations can expect to see improved response times, reduced downtime, and enhanced maintenance practices. A well-structured work order program encourages proactive rather than reactive maintenance, ultimately leading to cost savings and better resource allocation.
“An effective work order management strategy is foundational to operational success.”
Each sector can benefit from tailored solutions that meet their unique challenges. As technology continues to evolve, so too will the capabilities of work order programs, making them an integral part of future business strategy.